Value Stream Mapping – czym jest i jak mapować narzędzie?
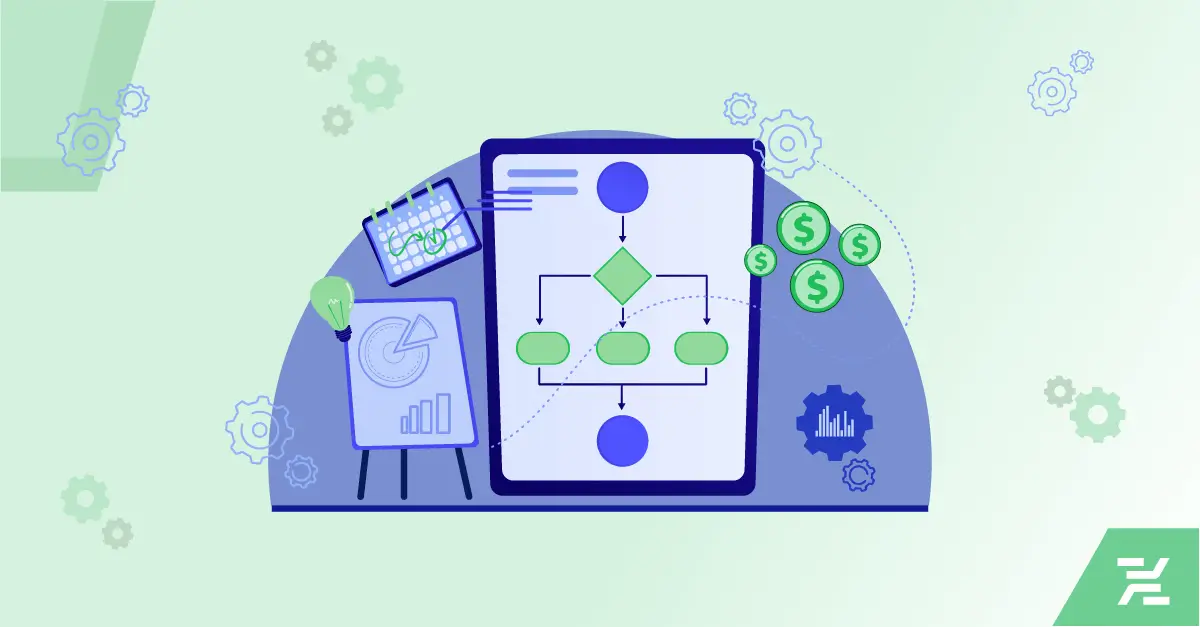
Value Stream Mapping to jedna z metod z zakresu lean management. Choć powstała w globalnej korporacji, jaką jest Toyota, to tak naprawdę może wykorzystać ją każda firma. Zarówno ta, która aktualnie doświadcza problemów w działaniu, jak i ta, która jest liderem w branży, ale wciąż chce się poprawiać. Czym dokładnie jest to narzędzie, jakie ma zalety oraz w jaki sposób je wykorzystywać? Serdecznie zachęcamy do lektury.
Spis treści
- Czym jest Value Stream Mapping?
- Historia metody Value Stream Mapping
- Do czego służy Value Stream Mapping i jakie ma zalety?
- Kiedy warto przeprowadzić Value Stream Mapping?
- Dlaczego warto stosować VSM?
- W jaki sposób tworzy się Value Stream Mapping?
- VSM krok po kroku
- Jak zrobić Value Stream Mapping, ale bez dużego nakładu pracy?
Czym jest Value Stream Mapping?
Value Stream Mapping, czyli inaczej Mapowanie strumienia wartości jest metodą graficznego przedstawienia składowych w procesach (zazwyczaj produkcyjnych). Celem jest przeanalizowanie wykonywanych kroków tak, aby później przeprowadzić niezbędne zmiany. Narzędzie to pozwala na zebranie wielu kluczowych informacji, w tym tego:
- jak zorganizowany jest proces,
- jaka jest w nim wartość dodana,
- czy są w nim źródła marnotrawstwa, a jeśli tak to jakie,
- jakie są dane wpływające do procesu oraz z niego wypływające,
- ile czasu zajmuje dany proces,
- jakie są ilości wykorzystywanych materiałów i surowców,
- ile osób bierze udział w poszczególnych czynnościach.
Historia metody Value Stream Mapping
Za pomysłodawców VSM uznaje się Taiichi Ohno i Shigeo Shingo, którzy byli zatrudnieni w Toyocie. Metodę tę stworzyli w roku 1980 w momencie, gdy zdali sobie sprawę, że skracając czas między kolejnymi etapami w procesie produkcyjnym, mogą poprawić produktywność i zmniejszyć ilość odpadów. Zalążki tego podejścia pojawiały się już jednak wcześniej, w tym na początku XX wieku. Aktualnie wykorzystuje się je przede wszystkim do komunikacji, strategicznego planowania, a także zmiany stylu zarządzania. Narzędzie można stosować także do bieżącego monitorowania procesów tak, aby szybko wychwycić potencjalne źródła zagrożeń, które szybko mogą przerodzić się w kryzysy.
Do czego służy Value Stream Mapping i jakie ma zalety?
Wykorzystanie Value Stream Mapping to w praktyce szereg korzyści. Najważniejsze spośród nich to:
- graficzne (a przez to łatwe do zrozumienia) ukazanie, jakie są powiązania w procesie,
- dostarczanie podstaw do opracowania planu działań doskonalących, które mogą być realizowane w celu usprawnienia procesu. Dzięki wizualizacji i analizie można zidentyfikować priorytety i podjąć konkretne działania mające na celu osiągnięcie pożądanych wyników,
- analiza wartości, gdyż VSM umożliwia dogłębną analizę ich przepływu, co pozwala na zidentyfikowanie kroków, które dodają wartość oraz tych, które tego nie robią,
- usprawnienie komunikacji i współpracy, gdyż VSM integruje różne działy i zespoły w organizacji, umożliwiając lepszą komunikację i zrozumienie całego przepływu wartości. Działa tym samym jako narzędzie wspólnego języka, które ułatwia identyfikację i rozwiązywanie problemów.
Jak doskonale widać, VSM nie tylko pozwala poszukać, ale i samo stanowi wartość dodaną i to na wielu różnych poziomach.
Kiedy warto przeprowadzić Value Stream Mapping?
Tak naprawdę metodę tę warto wykonywać w sposób regularny, aby stale poprawiać procesy w przedsiębiorstwie. Istnieje jednak kilka przypadków, gdy Value Stream Mapping jest szczególnie warte zastosowania.
Takim momentem jest sytuacja, gdy przedsiębiorstwo nie nadąża z realizacją zamówień. Dzięki takiej analizie mogą bowiem szybko unaocznić się obszary, w których możliwa jest względnie szybka poprawa, często bez gruntownych zmian.
Kolejnym przypadkiem jest sytuacja, gdy podmiot przestaje przynosić oczekiwane dochody oraz generuje nadmierne koszty. Być może proces trwa zbyt długo? Albo pojawiają się w nim czynniki hamujące, które negatywnie wpływają na poszczególne czynności? Dzięki takiej analizie również można je stosunkowo szybko wychwycić oraz zmienić procesy tak, aby firma znów była zyskowna.
Powyższe sytuacje określa się jednak jako krytyczne. Dlatego Value Stream Mapping może stanowić metodę prewencji, która pozwoli im zapobiec dzięki namierzeniu obszarów, które już dziś powodują pewne komplikacje i mogą one stać jeszcze bardziej destrukcyjne dla firmy w przyszłości.
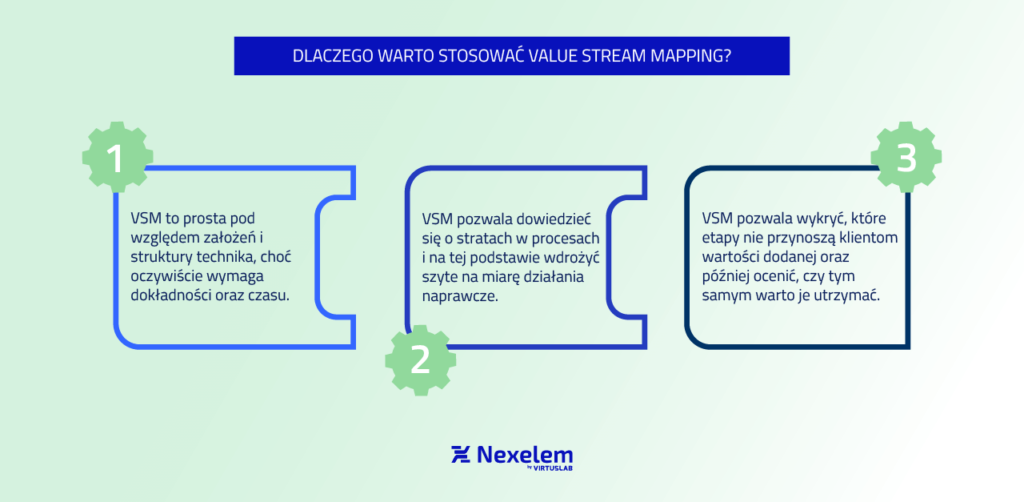
Dlaczego warto stosować mapowanie strumienia wartości?
Jest wiele powodów, dla których technika ta jest tak istotna oraz na stałe weszła do kanonu najskuteczniejszych metod lean management.
Po pierwsze jest prosta pod względem założeń i struktury, choć oczywiście wymaga dokładności oraz czasu, aby rzeczywiście uchwycić wszystkie istotne informacje o procesie.
Po drugie pozwala dowiedzieć się o stratach w procesach i na tej podstawie wdrożyć szyte na miarę działania naprawcze. Jej wykorzystanie wiąże się więc z konkretnymi korzyściami.
Po trzecie pozwala wykryć, które etapy nie przynoszą klientom wartości dodanej oraz później ocenić, czy tym samym warto je utrzymać.
Podsumowując, Value Stream Mapping to po prostu użyteczność. Wynika to również z faktu, że nie potrzeba drogich rozwiązań technologicznych, aby przeprowadzić taką pogłębioną analizę.
W jaki sposób tworzy się Value Stream Mapping?
Zasadniczo proces przebiega w trzech etapach:
- Analiza stanu aktualnego, czyli Value Stream Analysis, bez poddawania konkretnych etapów głębszej analizie. Na tym etapie często przeprowadza się Gemba Walk, czyli spacer po fabryce produkcyjnej pozwalający bliżej przyjrzeć się poszczególnym etapom.
- Stworzenie mapy tego, jaki ma być stan docelowy, czyli Value Stream Design. Ten etap jest momentem, gdy przedstawia się potencjalne rozwiązania.
- Tworzenie planu działań, czyli Value Stream Work Plan. To czas selekcji, czyli wyboru najlepszych i możliwych do wdrożenia rozwiązań.
Proces nie kończy się jedna na ewentualnych wdrożeniach. VSM warto bowiem regularnie powtarzać, gdyż – według lean management – proces doskonalenia nigdy się nie kończy i zawsze zostają elementy, które mogą wymagać poprawy.
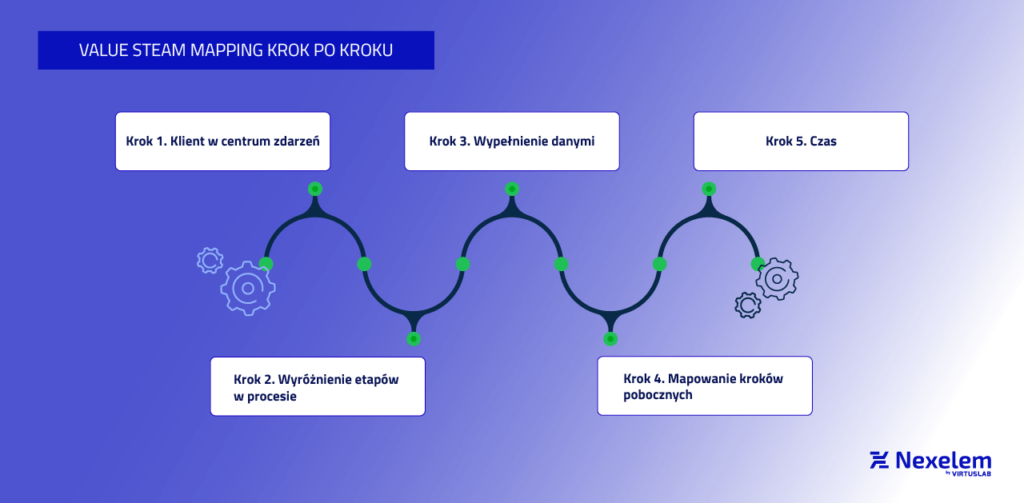
VSM krok po kroku
Mamy założenia oraz wiedzę teoretyczną, czas więc na konkrety, czyli to, co powinno zawierać Value Stream Mapping. Oto reguły, według których można stworzyć taką mapę.
Krok 1. Klient w centrum zdarzeń.
W praktyce to klient stanowi centrum zdarzeń w VSM. Dlatego jego symbol najlepiej umieścić w górnym rogu arkusza, wraz z określeniem, jakie jest jego zapotrzebowanie na produkty.
Krok 2. Wyróżnienie etapów w procesie.
Zajmujemy się wypisaniem poszczególnych etapów w naszym procesie, które będą oczywiście różnić się w zależności od przedsiębiorstwa.
Krok 3. Wypełnienie danymi.
Pod każdym etapem (segmentem) uzupełniamy informacje takie jak:
- liczba pracowników wymaganych do wykonania działania,
- cykl czasu,
- RFT (Right First Time), czyli ile spraw w ujęciu procentowym odbywa się bez problemów i trafia do kolejnego etapu,
- Batch size, czyli wielkość partii,
- Up Time procentowo określa czas, gdy pracownik lub maszyna są produktywni i czas ten ujmowany jest oczywiście bez przerw.
Krok 4. Mapowanie kroków pobocznych.
Bardzo często to tutaj tkwią źródła kosztów i problemów, czyli tych elementów, które opóźniają proces. To tzw. wybuchające gwiazdy, które najlepiej ująć na mapie tak, aby mocno się wyróżniały.
Krok 5. Czas
Kolejnym etapem jest wskazanie linii czasu dla procesu, czyli tego, ile trwają czynności oraz jakie są pomiędzy nimi przestoje.
Oczywiście mapowanie może różnić się w zależności od branży, w której działa firma i specyfiki jej działania. Można dodawać też do niego inne elementy oraz doskonalić.
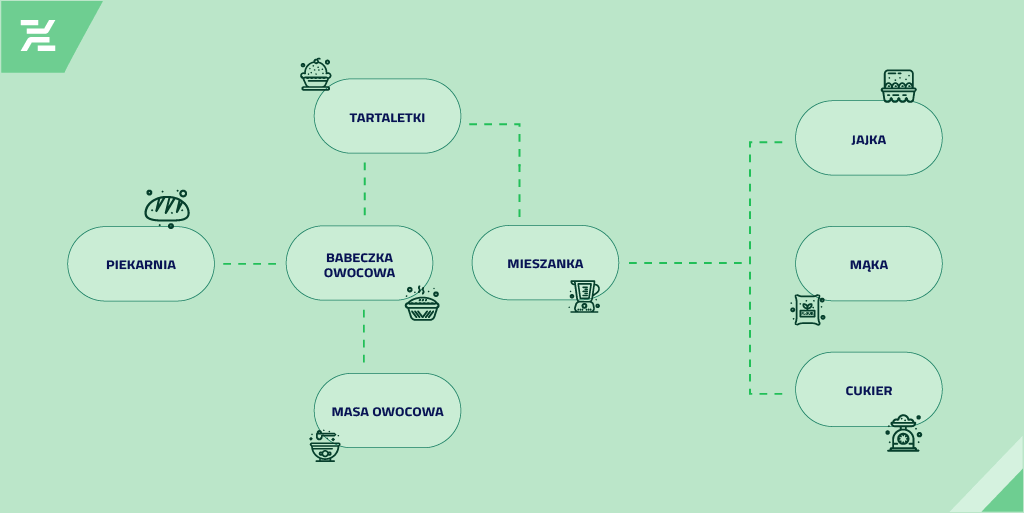
Jak przygotować Value Stream Mapping, ale bez dużego nakładu pracy?
Wykonanie VSM wymaga czasu, cierpliwości i dokładności. Co zrobić, gdy brakuje nam na to zasobów lub też procesy w firmie są niezwykle skomplikowane?
Okazuje się, że pomagają w tym nowoczesne technologie. Przykładem jest nasze oprogramowanie MES do zarządzania produkcją, w którym jedną z funkcjonalności jest tzw. graf zależności (można założyć, że jest to wizualizacja VMS). Jak opisać skomplikowaną rzeczywistość firmy czytelnym grafem? Tego można dowiedzieć się z naszego bloga, a zależności te są możliwe do odwzorowania nie tylko w przypadku dużych firm produkcyjnych, ale także mniejszych podmiotów, w których taka analiza będzie szybsza i łatwiejsza.
Decydując się na oprogramowanie MES firma ma do dyspozycji oczywiście nie tylko program Value Stream Mapping, ale również inne informacje, które pozwalają uczynić procesy bardziej efektywnymi. To m.in.:
- możliwość planowania produkcji wieloetapowej,
- predefiniowanie receptur,
- monitorowanie obciążenia gniazd produkcyjnych,
- generowanie zleceń na transporty wewnętrzne surowców,
- monitorowanie wydajności pracowników,
- śledzenie rentowności procesów produkcyjnych,
- łatwe i szybkie, ale i dokładne raportowanie.
Value Stream Mapping to metoda wciąż wykorzystywana zbyt rzadko w polskiej rzeczywistości gospodarczej. Jak jednak widać ma szereg zasad i może w stosunkowo krótkim czasie pomóc rozwiązać największe bolączki przedsiębiorstwa związane z procesami produkcyjnymi.
Interesują Cię inne narzędzia lean manufacturing? Jeśli tak, to koniecznie sprawdź naszego bloga i to, które są najskuteczniejsze oraz jakie są ich założenia.