Systemy produkcyjne
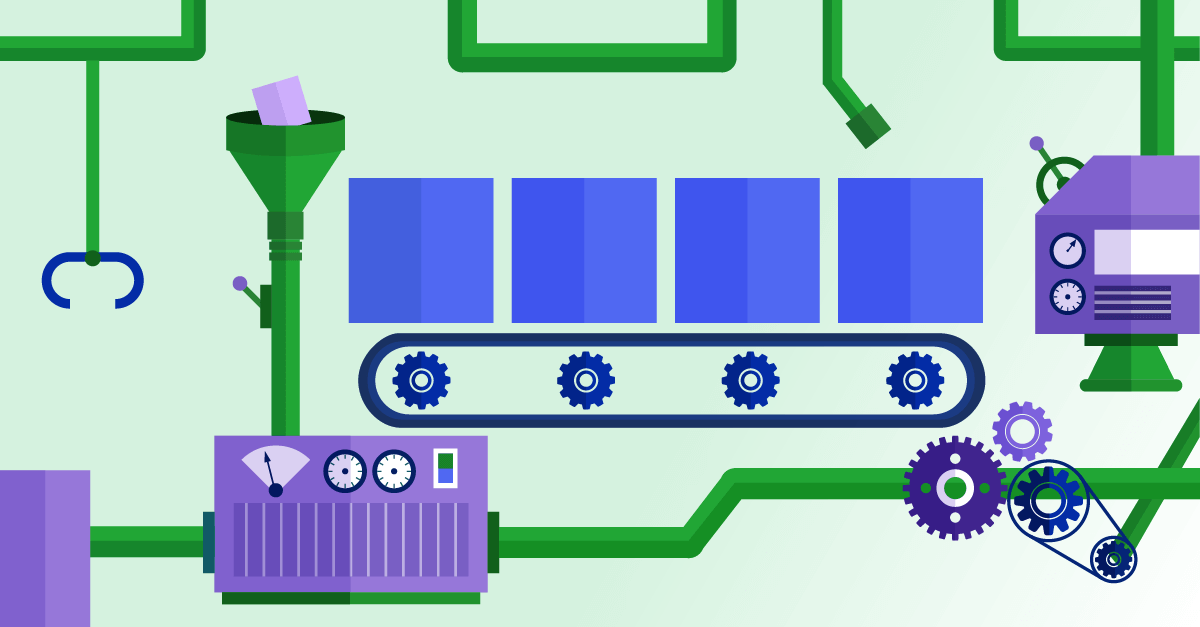
Niemal każdy sektor gospodarki opiera się na wykorzystaniu zaawansowanych technologii informatycznych. Branża produkcyjna nie jest tutaj wyjątkiem – wręcz przeciwnie, rosnąca konkurencja, coraz większe wymagania klientów oraz presja na skrócenie czasu dostaw sprawiają, że informatyzacja produkcji stała się nie tyle innowacyjną ciekawostką, co absolutną koniecznością. Jeśli chcemy pozostać konkurencyjni na rynku i uniknąć ryzyka zostania w tyle za bardziej dynamicznie rozwijającymi się graczami, wdrożenie systemów wspomagających produkcję to krok, którego nie da się pominąć.
Spis treści:
- Czym są systemy produkcyjne?
- Rola systemów produkcyjnych w nowoczesnym przedsiębiorstwie
- Najważniejsze systemy produkcyjne we współczesnych przedsiębiorstwach
- Jak właściwie wybrać systemy produkcyjne spośród dostępnych rozwiązań?
- Systemy produkcyjne. Podsumowanie
Warto jednak pamiętać, że „systemy produkcyjne” to określenie zbiorcze. Dotyczy szerokiego spektrum rozwiązań tworzonych z myślą o realizacji rozmaitych zadań. W dużych zakładach produkcyjnych, gdzie liczba maszyn i operatorów idzie w setki, wybór oprogramowania będzie znacząco inny niż w niewielkiej wytwórni działającej w modelu produkcji jednostkowej bądź małoseryjnej. Również same potrzeby przedsiębiorstw mogą być odmienne – jedni skupiają się na doskonaleniu planowania produkcji, inni na redukcji kosztów magazynowych, jeszcze inni chcą lepiej kontrolować jakość czy usprawnić przepływ dokumentów.
W dalszej części artykułu przyjrzymy się najważniejszym rodzajom systemów produkcyjnych i pochodnych rozwiązań wspierających produkcję. Jeśli jesteś właścicielem lub zarządzającym firmą produkcyjną i zastanawiasz się nad informatyzacją procesów – to właśnie doskonały moment, by pogłębić wiedzę o rozwiązaniach, które pomogą skutecznie zapanować nad całą ścieżką produkcyjną, od zamówienia materiałów aż po gotowy wyrób trafiający do rąk klienta.
Czym są systemy produkcyjne?
Systemy produkcyjne to zestaw narzędzi programistycznych i usług służących do planowania, monitorowania oraz optymalizacji procesów produkcji w przedsiębiorstwie. Integrują one dane z wielu obszarów działalności firmy – od zakupów, przez stany magazynowe i harmonogramowanie, aż po zarządzanie zasobami ludzkimi i raportowanie wyników. Ich głównym celem jest zapewnienie płynnego przepływu informacji i zwiększenie efektywności działań na linii produkcyjnej.
Rola systemów produkcyjnych w nowoczesnym przedsiębiorstwie
Wzrost efektywności – kluczowym zadaniem wszelkiego rodzaju systemów produkcyjnych jest minimalizacja strat związanych z przestojami, brakiem surowców czy błędnym planowaniem. Dzięki gromadzeniu danych w czasie rzeczywistym możliwe jest szybsze podejmowanie decyzji i natychmiastowa reakcja na nieprawidłowości.
Poprawa jakości wyrobów – solidne podstawy w postaci informacji o przebiegu procesu produkcyjnego (np. wskaźniki jakości, parametry maszyn) pozwalają ograniczyć ryzyko powstania wad. Przedsiębiorstwo jest w stanie wychwycić problemy wcześniej i wdrożyć działania korygujące.
Optymalizacja kosztów – zintegrowane systemy produkcyjne umożliwiają stałe śledzenie kosztów (materiałowych, energetycznych, związanych z przestojami) oraz identyfikowanie obszarów do poprawy w celu uzyskania maksymalnej wydajności przy minimalnych nakładach.
Zdolność adaptacji do zmian – dzięki automatycznym analizom i prognozom, przedsiębiorstwo może elastycznie reagować na zmiany popytu, awarie maszyn czy braki komponentów. System informatyczny wspiera także w dopasowaniu procesów do wymogów regulacyjnych czy standardów jakościowych.
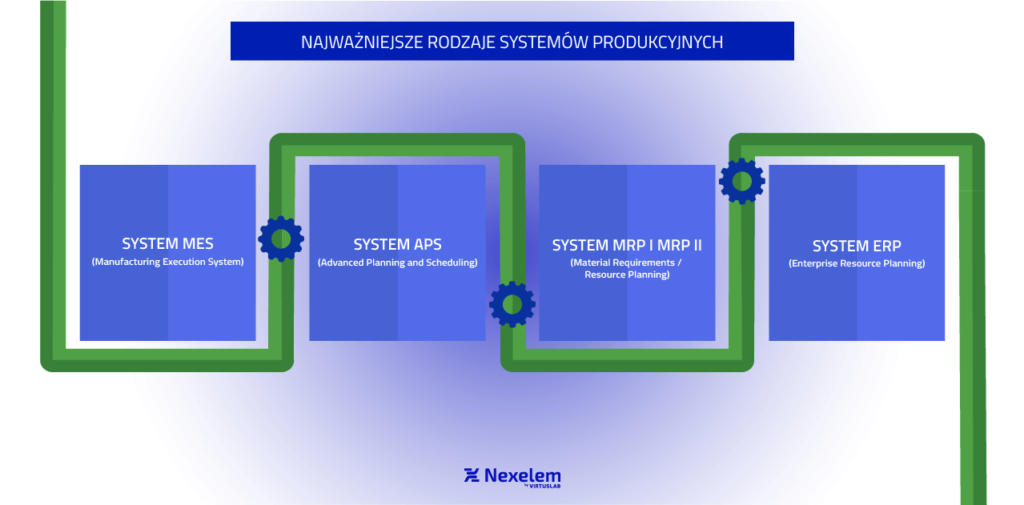
Najważniejsze rodzaje systemów produkcyjne we współczesnych przedsiębiorstwach
Wśród popularnych rozwiązań informatycznych wspierających działanie przedsiębiorstw produkcyjnych można wyróżnić kilka kategorii i rodzajów systemów produkcyjnych, które często wzajemnie uzupełniają się i można zintegrować je w kompleksowy ekosystem.
System MES (Manufacturing Execution System)
MES to system służący do nadzoru i kontroli nad procesem produkcyjnym w czasie rzeczywistym. Zajmuje się przede wszystkim poziomem operacyjnym produkcji, a więc bieżącym wykonywaniem zleceń:
- Monitorowanie produkcji: MES gromadzi dane bezpośrednio z maszyn, sensorów i stanowisk pracowniczych. Umożliwia to bieżącą kontrolę wskaźników, takich jak tempo pracy linii, liczba wyprodukowanych sztuk czy odsetek odrzuconych wyrobów.
- Zarządzanie zasobami i personelem: system wspiera przydzielanie zadań pracownikom, zarządzanie ich obciążeniem i ewidencję czasu pracy.
- Raportowanie i analiza: na podstawie informacji pozyskiwanych w czasie rzeczywistym, możliwe jest tworzenie raportów w celu szybkiej diagnozy problemów i podejmowania decyzji naprawczych.
- Integracja z innymi systemami: MES może współpracować m.in. z systemami APS, ERP czy MRP, stanowiąc źródło danych na temat stanu realizacji produkcji.
System APS (Advanced Planning and Scheduling)
APS to system, który koncentruje się na planowaniu i harmonogramowaniu produkcji, z uwzględnieniem zaawansowanych algorytmów optymalizacyjnych. Jego główną rolą jest precyzyjne ustalanie kolejności zadań produkcyjnych tak, by osiągnąć maksymalną wydajność przy jednoczesnym minimalizowaniu kosztów i czasu realizacji.
- Planowanie zasobów: APS uwzględnia dostępność maszyn, ludzi, surowców, półproduktów i infrastruktury magazynowej, generując szczegółowe plany produkcyjne.
- Prognozowanie popytu: na podstawie danych historycznych i aktualnych trendów rynkowych, APS jest w stanie przewidywać wolumen i rodzaj zapotrzebowania, co ułatwia strategiczne planowanie.
- Symulacje i scenariusze: system pozwala na tworzenie różnych wariantów planu i symulowanie skutków potencjalnych zmian, np. w przypadku awarii kluczowej maszyny lub nagłego wzrostu zamówień.
- Koordynacja z MES: dane z MES mogą być wykorzystywane przez APS do korekty planu na bieżąco, natomiast APS dostarcza MES informację o priorytetach produkcyjnych.
Systemy MRP i MRP II (Material Requirements/Resource Planning)
MRP i MRP II to jedne z najstarszych, ale wciąż często stosowanych koncepcji w przemyśle. Początkowo skupiały się głównie na planowaniu zapotrzebowania materiałowego; z czasem systemy ewoluowały w stronę MRP II, obejmując dodatkowo aspekty finansów, dystrybucji, zarządzania zasobami ludzkimi czy rozbudowane moduły planowania produkcji.
- Planowanie zapotrzebowania materiałowego: MRP oblicza, ile i kiedy przedsiębiorstwo potrzebuje surowców i półproduktów. Pozwala to uniknąć nadmiernego stanu magazynowego i zapewnić ciągłość produkcji.
- Kontrola terminów dostaw: system generuje rekomendacje dotyczące momentu zamawiania materiałów oraz śledzi realizację dostaw, by uniknąć opóźnień w procesie produkcji.
- Rozszerzone planowanie zasobów: MRP II uzupełnia tradycyjne funkcje MRP o planowanie mocy produkcyjnych, kosztów, przepływów finansowych oraz integrację z innymi działami firmy.
- Współpraca z systemem ERP: MRP i MRP II często stanowią część większych systemów ERP, które obejmują także sprzedaż, logistykę, kadry czy finanse.
System ERP dla produkcji (Enterprise Resource Planning)
ERP dla produkcji to rozbudowany system klasy biznesowej, integrujący wszystkie najważniejsze obszary funkcjonowania przedsiębiorstwa – od produkcji i magazynowania, przez sprzedaż, aż po kadry i finanse. W kontekście przedsiębiorstw produkcyjnych najważniejsza będzie elastyczność ERP oraz dostępność modułów ściśle dedykowanych obsłudze procesów produkcyjnych.
- Jedna baza danych: w ERP wszystkie informacje są przechowywane w spójnej bazie, co eliminuje powielanie danych oraz ryzyko sprzecznych informacji w różnych częściach przedsiębiorstwa.
- Planowanie i harmonogramowanie: systemy ERP dla produkcji zawierają moduły integrujące funkcje MRP/MRP II oraz APS, umożliwiając harmonogramowanie i kontrolę realizacji produkcji w jednym miejscu.
- Zarządzanie łańcuchem dostaw: ERP wspiera pełny przepływ surowców i produktów – od dostawców, przez proces produkcyjny, aż do ostatecznego odbiorcy. Analiza danych w czasie rzeczywistym pomaga w podejmowaniu szybkich decyzji o zmianach w logistyce.
- Automatyzacja procesów biznesowych: system ERP może obejmować procesy kadrowe (HR), finansowe, sprzedażowe (CRM), zarządzanie dokumentacją i obiegiem pracy (workflow), co usprawnia pracę zespołu i obniża koszty operacyjne.
Jak właściwie wybrać systemy produkcyjne spośród dostępnych rozwiązań?
Wdrożenie systemów produkcyjnych to jedna z najważniejszych decyzji, przed którymi stoi każda firma nastawiona na wytwarzanie fizycznych produktów. Aby jednak osiągnąć realne korzyści, warto zainwestować w oprogramowanie, które będzie kompleksowe, elastyczne i odpowiednio dopasowane do specyfiki przedsiębiorstwa.
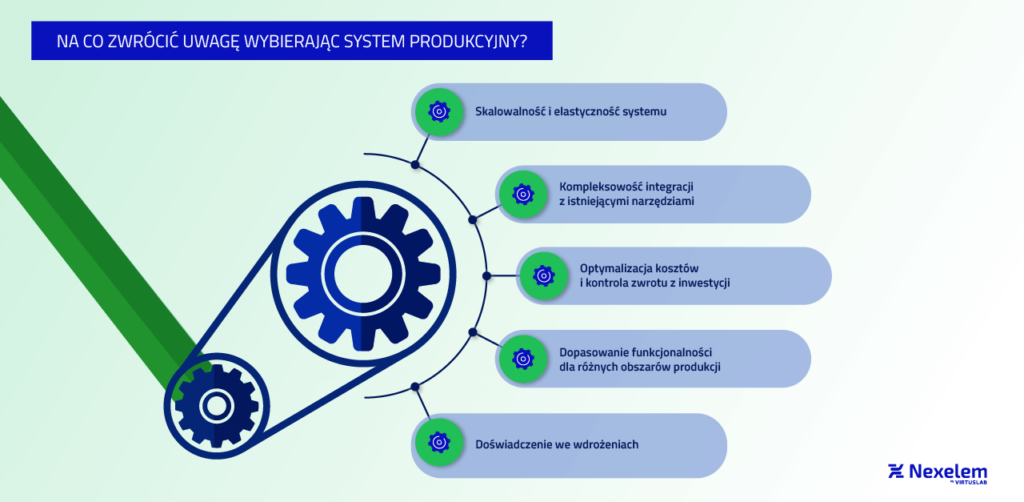
Skalowalność i elastyczność systemu
System informatyczny powinien rosnąć razem z przedsiębiorstwem. Systemy produkcyjne Nexelem oferuje modułowe rozwiązania, które można wdrażać etapami, dopasowując zakres i funkcjonalność do bieżących potrzeb. Dzięki temu unikamy ryzyka nadmiernego obciążenia budżetu i jednocześnie mamy pewność, że w razie wzrostu skali działalności łatwo dołożymy kolejne elementy.
Dostosowanie do różnych branż i procesów to kolejny ważny punkt. Oprogramowanie Nexelem jest konfigurowalne i może być implementowane w przedsiębiorstwach o zróżnicowanych modelach produkcji (masowej, seryjnej, jednostkowej czy projektowej). Warto wybrać rozwiązanie z wysoki poziomem personalizacji, które sprawa, że funkcjonalności dopasujemy zarówno do dużych fabryk, jak i mniejszych zakładów.
Kompleksowa integracja z istniejącymi narzędziami
- Połączenie z obecnym parkiem maszynowym: nowoczesna produkcja często oparta jest na rozwiązaniach Przemysłu 4.0, wykorzystujących czujniki IIoT czy integrację z systemami SCADA. Rozwiązania mogą być łatwo zsynchronizowane z istniejącą infrastrukturą, co umożliwia płynną wymianę danych i minimalizuje przerwy w działaniu.
- Sprawne wdrożenia: każdy proces implementacji oprogramowania wiąże się z ryzykiem przestojów czy przejściowych trudności. Nexelem, bazując na swoich doświadczeniach we wdrożeniach, zapewnia kompleksowe wsparcie na każdym kroku – od analizy wymagań, przez przygotowanie prototypu, aż po szkolenia personelu i uruchomienie pełnej wersji systemu.
- API i komunikacja: rozwiązania Nexelem wyposażone są w otwarte interfejsy (API), dzięki czemu mogą być łączone z innymi używanymi już w firmie aplikacjami, np. z obszaru logistyki, księgowości czy CRM. To pozwala uniknąć problemów z synchronizacją danych i zapewnia pełną transparentność w całym przedsiębiorstwie.
Optymalizacja kosztów i kontrola zwrotu z inwestycji
- Przejrzysta struktura licencji: Przy doborze systemu warto z góry ustalić, jakie będą koszty wdrożenia, utrzymania i rozbudowy oprogramowania. Nexelem oferuje elastyczne modele licencyjne oraz możliwość etapowego wdrażania, co ułatwia przedsiębiorstwom zachowanie płynności finansowej.
- Wsparcie w analizie TCO: Całkowity koszt posiadania (często określany angielską nazwą, czyli Total Cost of Ownership) obejmuje nie tylko cenę zakupu, ale i rozliczne wydatki na serwis, aktualizacje czy modyfikacje. Dzięki narzędziom i raportom, jakie udostępnia Nexelem, można na bieżąco kontrolować wszystkie aspekty kosztowe oraz prognozować ROI (Return on Investment).
- Redukcja strat produkcyjnych: Główna wartość rozwiązań typu MES i APS polega na lepszej organizacji pracy oraz eliminacji marnotrawstwa surowców.
Dopasowane funkcjonalności dla różnych obszarów produkcji
- Precyzyjne sterowanie procesem (MES): System MES od Nexelem umożliwia monitorowanie parametrów wytwarzania w czasie rzeczywistym. Dzięki temu managerowie produkcji mogą w porę reagować na odchylenia od norm czy pojawiające się problemy na liniach produkcyjnych.
- Zaawansowane planowanie i harmonogramowanie (APS): Rozwiązanie APS Nexelem sprawdza się tam, gdzie niezbędna jest dynamiczna alokacja zasobów. Dzięki algorytmom optymalizacji można znacząco skrócić czas przestojów, kolejki produkcyjne i wykorzystać potencjał parku maszynowego w maksymalnym stopniu.
- Efektywne zarządzanie zapasami i zamówieniami (MRP/MRP II): Funkcje MRP/MRP II zintegrowane z ERP Nexelem wspierają bieżące bilansowanie surowców i materiałów. Umożliwiają generowanie terminowych zamówień i kontroli nad stanami magazynowymi, co zapobiega zarówno niedoborom, jak i kosztownym nadwyżkom.
- Kompleksowa koordynacja przedsiębiorstwa (ERP): Dzięki bogatej ofercie ERP Nexelem można zarządzać nie tylko samymi procesami wytwórczymi, ale też obszarami finansów, kadr czy sprzedaży. Centralna baza danych i spójna logika systemu pozwalają eliminować powielanie informacji między działami.
Zaufanie i doświadczenie we wdrożeniach
- Udokumentowane historie sukcesu: sprawdź case studies wdrożeń w firmach, które dzięki wdrożeniu rozwiązań Nexelem znacząco poprawiły wydajność, obniżyły koszty i usprawniły przepływ informacji.
- Stałe wsparcie serwisowe: zapewniamy instalację systemu, konfigurację i długofalową opiekę posprzedażową. Pomoc w rozwoju i aktualizacjach oprogramowania jest kluczowa dla utrzymania pełnej sprawności, zwłaszcza w dynamicznie rosnących przedsiębiorstwach.
- Partnerskie podejście: dążymy do tego, by proponowane rozwiązania nie tylko działały na papierze, ale realnie odzwierciedlały procesy zachodzące w firmie. Podczas analizy przedwdrożeniowej staramy się poznać szczegółowo strukturę przedsiębiorstwa, aby zaproponować najbardziej trafne i przyszłościowe opcje.
Systemy produkcyjne. Podsumowanie
Wdrożenie nowoczesnego systemu produkcyjnego jest kluczowym elementem cyfrowej transformacji w przedsiębiorstwach działających w sektorze przemysłowym. Integracja danych, automatyzacja, sprawne planowanie i monitorowanie produkcji to fundamenty, które decydują o konkurencyjności na dynamicznych rynkach.
Rozbudowane rozwiązania, takie jak MES, APS, MRP/MRP II czy ERP, są w stanie odpowiadać na potrzeby zarówno małych warsztatów, jak i dużych fabryk, dzięki modularnej budowie i elastyczności konfiguracji. Wybór konkretnego rozwiązania powinien bazować na analizie potrzeb, budżetu, oczekiwań względem ROI oraz przyszłych kierunków rozwoju.
Systemy produkcyjne mogą i powinny działać jako uzupełniające się elementy jednego, spójnego ekosystemu. Właściwe wdrożenie takiego rozwiązania stanowi duży krok w stronę pełnej automatyzacji i kontroli nad procesami produkcyjnymi, co w konsekwencji przekłada się na wzrost wydajności, redukcję kosztów i lepsze wykorzystanie zasobów.