Przemysł 4.0 – czym jest czwarta rewolucja przemysłowa?
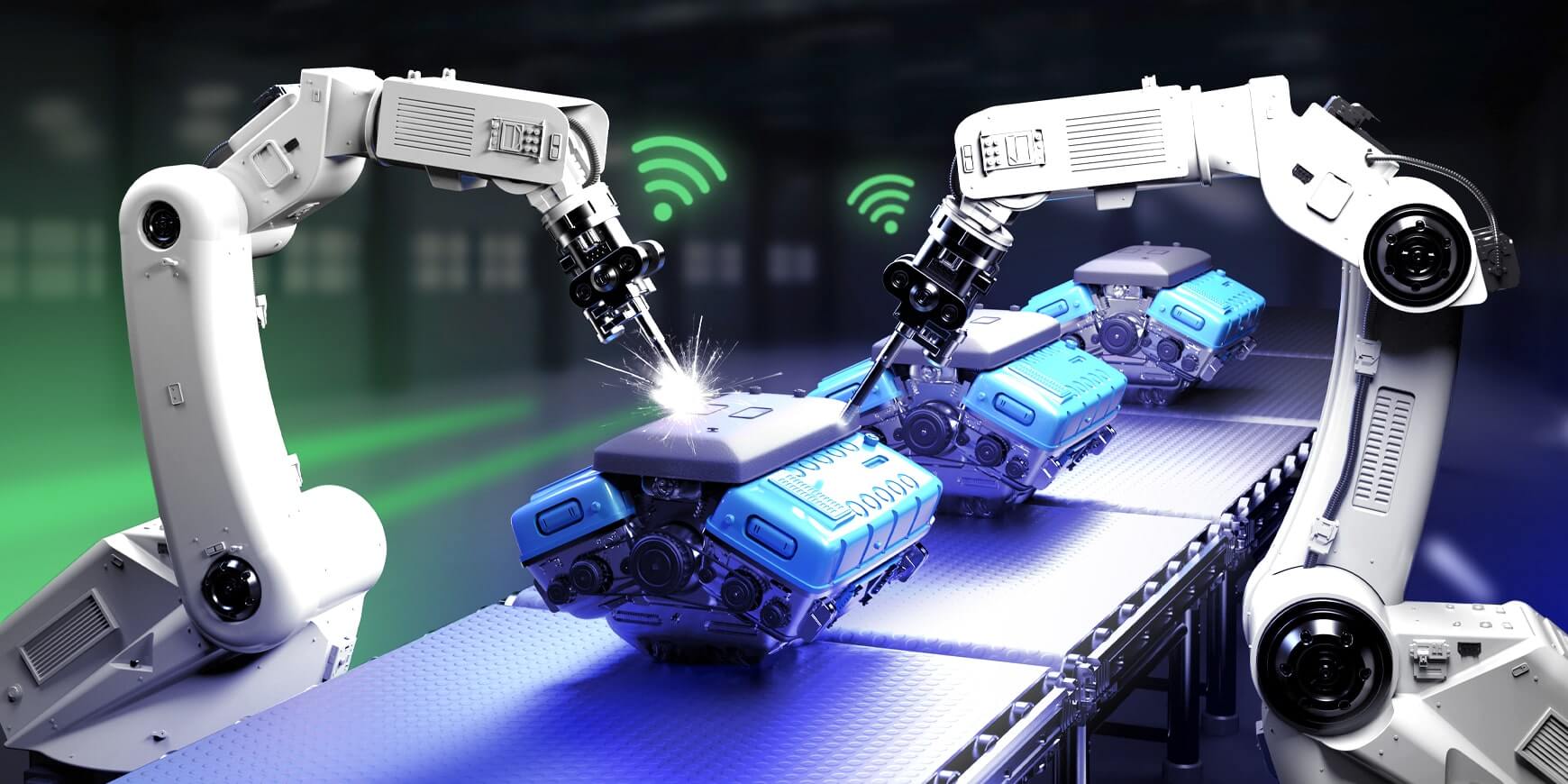
Cechą charakterystyczną rewolucji przemysłowej jest stworzenie przełomowej technologii, która na nowo definiuje sposób produkcji i metody pracy. Trzy poprzednie związane były z wynalezieniem: maszyny parowej, linii produkcyjnej oraz komputera. Obecnie jesteśmy w trakcie czwartej rewolucji przemysłowej, nazywanej również Przemysłem 4.0 (Industry 4.0). Termin ten określa zmiany społeczne, przemysłowe i technologiczne wywołane cyfrową transformacją przemysłu. Nadaje ona nowe oblicze automatyzacji i monitorowaniu łańcucha dostaw, dzięki wykorzystaniu inteligentnych technologii. Sprawdź, czym jest przemysł 4.0.
Spis treści:
- Rewolucja przemysłowa – kontekst historyczny przemysłu 4.0
- Przemysł 4.0 – co to jest?
- Przykłady zastosowania Przemysłu 4.0
- Jakie są korzyści z wdrożenia Przemysłu 4.0 w firmie?
Rewolucja przemysłowa – kontekst historyczny przemysłu 4.0
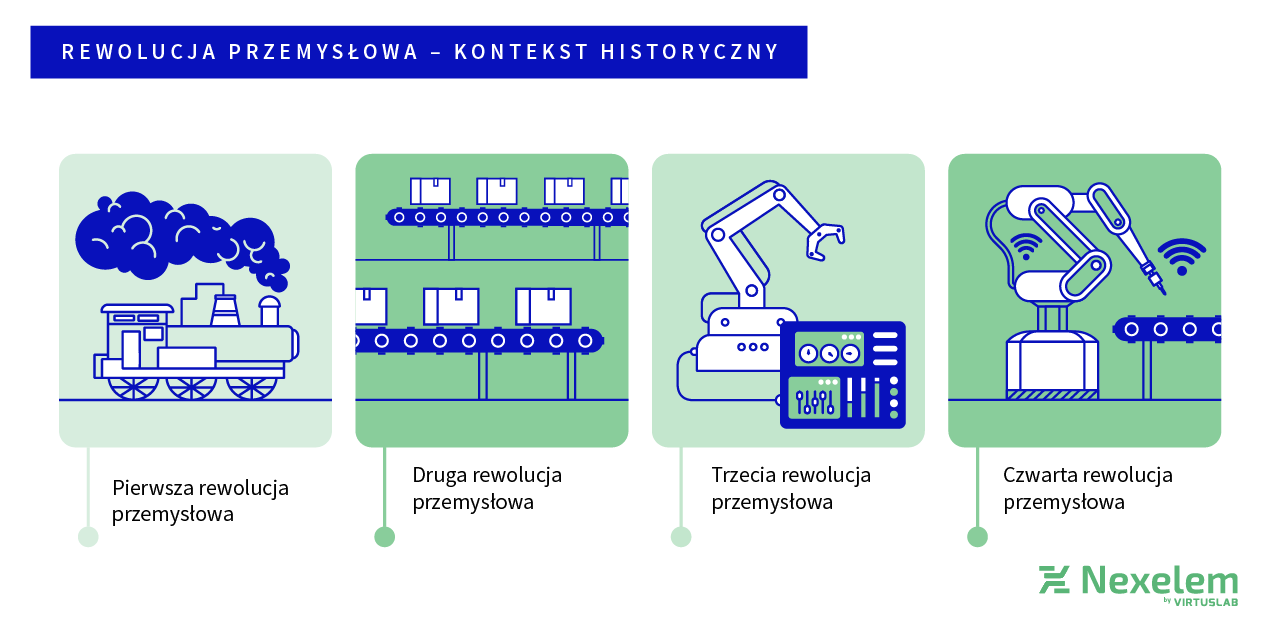
Termin rewolucja definiuje gwałtowną i radykalną zmianę. W historii miała miejsce, gdy nowe technologie wraz z nowym sposobem postrzegania świata powodowały głęboką zmianę w systemach gospodarczych i strukturach społecznych.
- Pierwsza rewolucja przemysłowa trwała od 1760 i zakończyła się roku 1840. Zapoczątkowana została w chwili wynalezienia silnika parowego, co spowodowało budowę kolei oraz przyczyniło się do wprowadzenia produkcji mechanicznej. Nić, która do tej pory wytwarzana była ręcznie na krosnach, dzięki mechanizacji zaczęła być produkowana osiem razy szybciej, dzięki zastosowaniu silników parowych. Wykorzystanie pary do celów przemysłowych było największym przełomem w dziejach ludzkiej produkcji. Kolejne lata to wynalazki parowca i parowozu, które umożliwiły przewożenie towarów na znaczne odległości w zdecydowanie krótszym czasie. Wszystko to przyczyniło się do jeszcze bardziej dynamicznego rozwoju cywilizacji.
- Druga rewolucja przemysłowa rozpoczęła się na przełomie XIX i XX wieku wraz z wynalezieniem elektryczności i linii produkcyjnej, dzięki czemu możliwa była produkcja na skalę masową. Pierwsza linia korzystająca z energii elektrycznej powstała w roku 1870. Henry Ford zaczerpnął pomysł masowej produkcji i zreorganizował pracę przy montażu samochodów, co radykalnie zmieniło branżę. Wcześniej samochód składany był na jednym stanowisku, a od tamtego momentu produkowano go etapami na przenośniku. Efektem było znaczne przyspieszenie procesu i obniżenie kosztów. Kolejne lata to czas, w którym Thomas Edison udoskonalił prądnicę i opatentował żarówkę elektryczną, dzięki czemu światło zaczęło docierać do domów.
- Trzecia rewolucja przemysłowa rozpoczęła się w latach 60. XX wieku. Zapoczątkowana została pojawieniem się kolejno: półprzewodników i dużych systemów komputerowych (lata 60.), komputerów osobistych (lata 70-80.) oraz internetu (lata 90.). Wdrożenie programowalnych sterowników z pamięcią i komputerów umożliwiło automatyzację całego procesu produkcji. Od tej pory może odbywać się bez udziału człowieka. Przykładem zastosowania tego podejścia jest wykorzystanie robotów, które po zaprogramowaniu sekwencji czynności wykonują zadania bez ludzkiej interwencji.
- Czwarta rewolucja przemysłowa trwa obecnie. Jej bazą są poprzednie osiągnięcia. Polega na tym, że skomputeryzowane systemy produkcji wyposaża się dodatkowo w łącza sieciowe, a więc wykorzystuje się technologie informacyjne i komunikacyjne w przemyśle. Daje to możliwość komunikacji z innymi obiektami oraz przekazywanie informacji o samych urządzeniach. Połączenie wszystkich systemów prowadzi do powstania inteligentnych fabryk, w których systemy produkcji komponenty i ludzie komunikują się za pośrednictwem sieci. Produkcja odbywa się zatem prawie autonomicznie.
Przemysł 4.0 – co to jest?
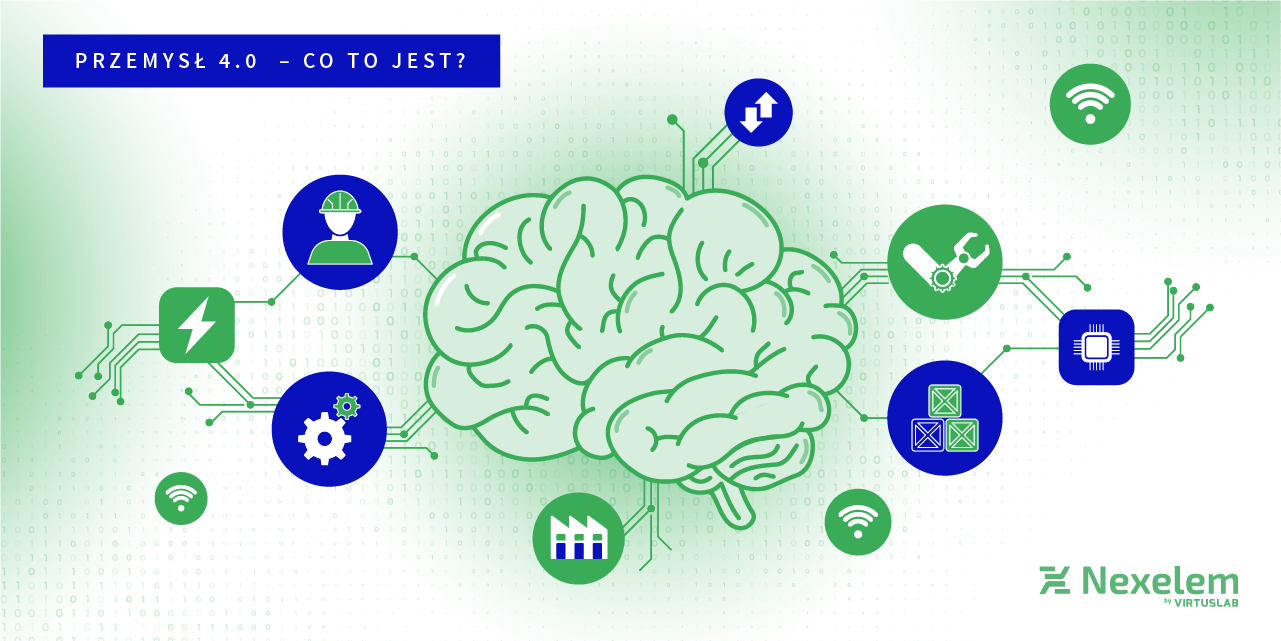
Termin przemysł 4.0 po raz pierwszy został użyty podczas targów międzynarodowych Hannover Messe już w 2011 roku, kiedy zaprezentowano projekt opracowany przez niemiecki rząd. Czwarta rewolucja przemysłowa jest podstawą cyfrowej transformacji każdej firmy. U jej podstaw leżą przemysłowy Internet rzeczy (IoT) oraz autonomiczne układy, które wykorzystują algorytmy komputerowe do monitorowania oraz sterowania elementami fizycznego otoczenia tj. maszyny, roboty lub pojazdy. W wyniku tego każdy element łańcucha dostaw (produkcja, logistyka, magazynowanie) staje się “inteligentny”. Dodatkowo wzrasta poziom przejrzystości procesów i kontroli nad nimi.
Czwarta rewolucja przemysłowa zmierza do integracji zasobów materialnych i cyfrowych poprzez wykorzystanie możliwości, które aktualnie we wszystkich dziedzinach życia dostarczane są za pomocą danych, narzędzi analitycznych i technologii mobilnych. Poprzednie rewolucje przemysłowe obejmowały życie kilku pokoleń. Obecnie łączność bezprzewodowa, automatyzacja, sztuczna inteligencja, nanotechnologia, czy big data przyjmują niespotykane do tej pory tempo rozwoju. Wszystko to zmienia nie tylko nasze życie i pracę, ale również relacje międzyludzkie.
Przemysł 4.0 to integracja inteligentnych maszyn, systemów i sposobu wprowadzenia zmian w procesach produkcyjnych. Wszystko po to, aby osiągać lepszą wydajność. Wpływ rewolucji przemysłowej na działalność przedsiębiorstw jest ogromny. Zmienił się nie tylko sposób pracy, ale również rola ludzi.
Ogłoszenie:
Czy Twoja produkcja jest gotowa na Industry 4.0 – Webinar
Jeżeli interesuje Cię koncepcja Industry 4.0 i wykorzystanie danych na produkcji, cyfryzacja oraz technologie AI / ML, dzięki którym można produkować efektywniej i zwiększyć marżowość firmy to zapisz się na nasz bezpłatny webinar. Poruszamy w nim następujące tematy:
- Krótko o Przemyśle 4.0
- Recepta na Przemysł 4.0?
- Czym jest transformacja cyfrowa?
- Czym jest sztuczna inteligencja (AI / ML /DL) ?
- Jak zbierać i wykorzystywać dane [produkcyjne]?
- Jak NIE prowadzić cyfryzacji?
- Kiedy używać technologii AI na produkcji?
- Nasze przykłady użycia analizy danych (Big-Data).
Jakie technologie napędzają Przemysł 4.0?
Przemysł 4.0 to rewolucja w sposobie wytwarzania, ulepszania i dystrybucji produktów. Firmy integrują technologie wspomagające, tj. internet rzeczy, przetwarzanie w chmurze, sztuczną inteligencję i uczenie maszynowe w swoich zakładach produkcyjnych.
Inteligentne fabryki wykorzystują zaawansowane oprogramowanie i robotykę, aby gromadzone dane umożliwiały podejmowanie lepszych decyzji. Zwiększona automatyzacja prowadzi do nowego poziomu wydajności i responsywności wobec klientów.
W konsekwencji osiągamy wyższą produktywność i lepszą jakość. Zmniejsza się również liczba błędów produkcyjnych, co daje większość oszczędność czasu i pieniędzy. Istotne jest to, że technologie Przemysłu 4.0 mogą być stosowane we wszystkich rodzajach przedsiębiorstw przemysłowych. Do najważniejszych z nich zaliczamy:
Internet rzeczy
Internet rzeczy (ang. IoT Internet of Things) – w uproszczeniu oznacza system urządzeń elektronicznych umożliwiający automatyczną komunikację i wymianę danych za pomocą sieci, czyli bez ingerencji człowieka.
IOT powiązany jest z IIoT (ang. Industrial Internet of Things), który oznacza Przemysłowy Internet Rzeczy. Są to dwie główne technologie w cyfrowej rewolucji. IoT będąc siecią połączonych urządzeń, daje im możliwość komunikowania się ze sobą i udostępniania danych użytkownikom poprzez internet. Jego częścią w fabryce może być wszystko: maszyny, podstacje elektryczne, budynki, infrastruktura.
Tak naprawdę liczba połączonych urządzeń zwiększa się każdego dnia. IoT gromadzi dane z różnych źródeł, a następnie przesyła wynik do centralnego systemu za pomocą internetu. Dzięki temu kadra zarządzająca podejmuje szybsze i bardziej trafne decyzje. Może również przewidzieć przyszłe efekty. Technologię tę można wykorzystać do automatyzacji sprzętu oraz części realizowanych operacji. Inteligentne czujniki, w które wyposażony jest sprzęt, mogą dostosowywać działanie, aby przykładowo optymalizować zużycie energii. Najprostszym przykładem są światła aktywowane za pomocą ruchu.
Przetwarzanie w chmurze
Przetwarzanie w chmurze – stanowi fundament właściwie każdej strategii Przemysłu 4.0. Inteligentna produkcja do pełnej realizacji wymaga łączności i integracji produkcji, łańcucha dostaw, sprzedaży oraz usług.
Możliwe jest to właśnie poprzez zastosowanie chmury, dzięki której proces przechowywania oraz analizowania danych jest bardziej wydajny i ekonomiczny. Chmura stanowi realne obniżenie kosztów początkowych małych i średnich producentów. Przetwarzanie w chmurze polega na udostępnieniu zasobów obliczeniowych w postaci aplikacji po centra przetwarzania danych na żądanie za pośrednictwem internetu. Płaci się za faktyczne wykorzystanie. Dostęp do wszystkich potrzebnych zasobów IT jest samoobsługowy. Aplikacje w chmurze działają na tzw. komputerach „w chmurze” należących do dostawców usług i przez nich są utrzymywane. Użytkownicy łączą się z nimi najczęściej za pomocą przeglądarki internetowej.
AI i uczenie maszynowe
AI i uczenie maszynowe – sztuczna inteligencja pozwala maszynom uczyć się na podstawie doświadczeń, dzięki czemu firmy produkcyjne mogą w pełni wykorzystać cały wolumen informacji generowanych w hali produkcyjnej, jednostkach organizacyjnych, u partnerów i innych źródłach zewnętrznych.
AI umożliwia generowanie informacji w zakresie widoczności, automatyzacji i przewidywalności procesów biznesowych. Przykładem mogą być awarie w trakcie procesu produkcyjnego, które wykorzystywane są do zbierania informacji, aby na tej podstawie wykonywać konserwacje predykcyjne oparte na algorytmach uczenia się maszynowego.
Poprawia to ciągłość działania i wydajność maszyn. AI opiera się na potencjale jednostek obliczeniowych odtwarzających ludzki sposób uczenia się najpierw poprzez naśladownictwo, a następnie przez analizę. Dzięki temu maszyny wykonują zadania przypisane człowiekowi. Rozwiązanie to jest coraz częściej stosowane w produkcji i przemyśle. Sprawdza się podczas projektowania, ulepszania procesów, zapobieganiu zużycia maszyn, jak również do optymalizacji wykorzystywanej energii. Odgrywa też ważną rolę w procesie kontroli jakości.
Z badań przeprowadzanych w okresie pandemii 74% badanych firm potwierdziło, że rozwiązania związane ze sztuczną inteligencją okazały się przydatne. Inwestycja w cyfryzację i sztuczną inteligencję to aktualny kierunek rozwoju większości przedsiębiorstw.
Przetwarzanie brzegowe
Przetwarzanie brzegowe – wymogi związane z działaniami produkcyjnymi w czasie rzeczywistym w niektórych przypadkach oznaczają analizę danych już w momencie ich tworzenia, czyli na tzw. brzegu. Dzięki temu możliwa jest minimalizacja czasu oczekiwania od momentu wygenerowania danych do czasu, kiedy wymagana jest reakcja. Przykładem może być wykrycie błędu związanego z bezpieczeństwem, które wymaga wykonania czynności przy użyciu sprzętu w czasie rzeczywistym. W tym przypadku czas przesłania danych do chmury przedsiębiorstwa i z powrotem do hali produkcyjnej jest zbyt długi. Uzależniony jest też od stabilności sieci. Przetwarzanie brzegowe zdecydowanie zmniejszy zagrożenie bezpieczeństwa. Zaletą jest więc szybszy dostęp do spostrzeżeń, krótsze czasy odpowiedzi i udoskonalone wykorzystanie przepustowości. Dane są przetwarzane i analizowane bliżej punktu, w którym powstają, dzięki czemu skraca się czas ich dostarczania.
Cyberbezpieczeństwo
Cyberbezpieczeństwo – znaczenie cyberbezpieczeństwa w firmach produkcyjnych jest coraz większe. Technologia operacyjna, czyli łączność sprzętu operacyjnego w fabryce lub terenie z jednej strony umożliwia wydajniejsze procesy produkcyjne. Z drugiej strony ujawnia ścieżki dostępu dla złośliwego oprogramowania. Cyfrowa transformacja w kierunku Przemysłu 4.0 musi opierać się na cyberbezpieczeństwie. Konieczne jest wprowadzenie odpowiednich środków bezpieczeństwa danych i usług chmurowych. Przechowywane dane należy szyfrować i aktualizować oprogramowania. W Unii Europejskiej wprowadzana jest obowiązkowa certyfikacja i akredytacja, która obejmuje urządzenie IoT. Na producentów nakłada się minimalne wymagania dotyczące bezpieczeństwa. W tym kontekście bardzo ważna jest świadomość zagrożeń zarówno wśród kadry zarządzającej, jak i pracowników przedsiębiorstw. Stawką jest nie tylko utrata danych, ale również narażenie prywatności.
Cyfrowy bliźniak
Cyfrowy bliźniak – z ang. digital twin to inaczej wirtualna replika procesów, linii produkcyjnych, fabryk i łańcuchów dostaw. Powstaje w trakcie pobierania danych z czujników IoT, sterowników PLC i innych urządzeń podłączonych do internetu. Cyfrowe bliźniaki wykorzystywane są przez producentów do zwiększena produktywności. W ten sposób usprawnia się przepływ pracy i projektuje nowe produkty. Symulacja procesów produkcyjnych wykorzystywana jest do testowania zmian w procesie. Przyczynia się do opracowania metod zmniejszania przestojów oraz podnoszenia zdolności produkcyjnej. Stałe monitorowanie produktu i jego reakcji pozwala na ciągłe ulepszanie i eliminację występujących błędów. Optymalizacja pozwala uzyskać doskonalszy produkt. Cyfrowy bliźniak zmienia sposób zarządzania i funkcjonowania przedsiębiorstwa. Przekłada się to na korzyści ekonomiczne dla przedsiębiorstwa i sprawia, że zakład jest bardziej konkurencyjny na rynku.
Przykłady zastosowania Przemysłu 4.0
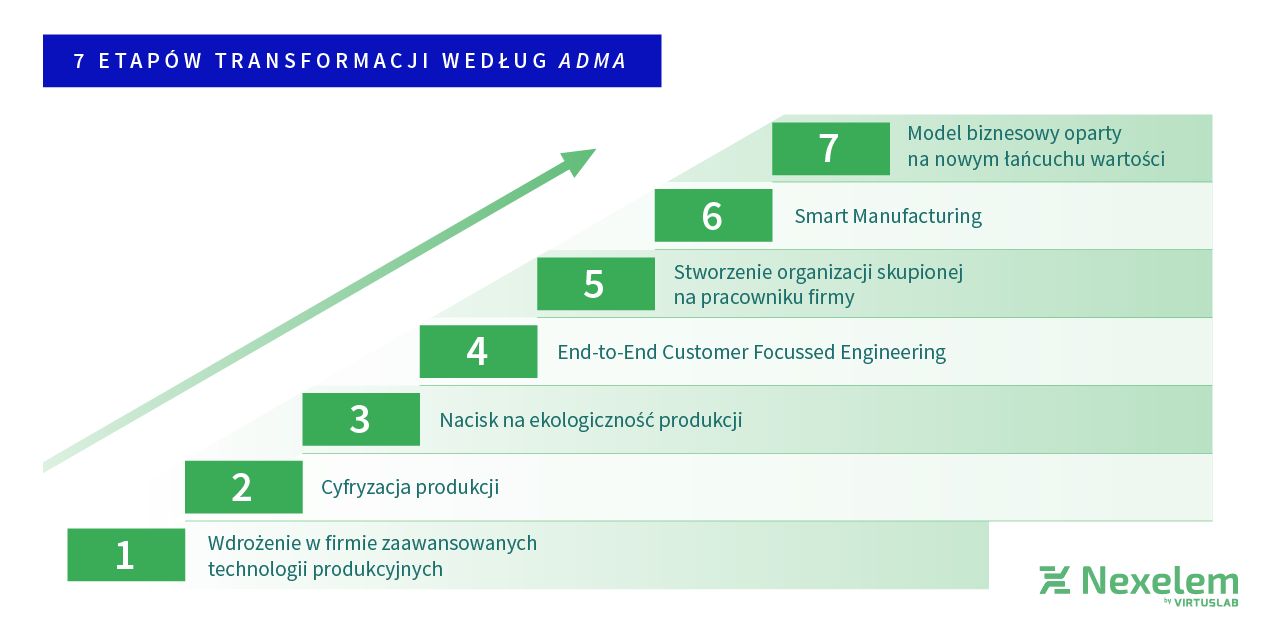
Pojawienie się technologii cyfrowych obok przełomowych rozwiązań w produkcji materiałów i biotechnologii prowadzi do powstania zupełnie nowych metod produkcji, komunikacji, konsumpcji i przemieszczania się. Zmiany te mają fundamentalne znaczenie dla aktualnie występujących gałęzi przemysłu. Wpływają nie tylko na największych graczy rynkowych, ale również na całą światową gospodarkę z uwzględnieniem lokalnych społeczności i tożsamości poszczególnych osób.
Za rozwój i wdrażanie elementów Przemysłu 4.0 odpowiedzialne jest Europejskie Centrum Wsparcia Zaawansowanej produkcji (ADMA) powołane przez Komisję Europejską. Ma to ułatwić przedsiębiorcom dostęp do specjalistycznej wiedzy z zakresu technologii i organizacji. Według ADMA przykłady transformacji w kierunku przemysłu 4.0 obejmują siedem etapów:
- Wdrożenie w firmie zaawansowanych technologii produkcyjnych – elastyczne systemy produkcyjne mają ułatwić szybkie dostosowywanie się do zmian w zakresie liczby lub kategorii produktów.
- Cyfryzacja produkcji – ludzie, maszyny i produkty muszą ze sobą współdziałać,
- Nacisk na ekologiczność produkcji, np. poprzez wykorzystanie odnawialnych źródeł energii, pełne wykorzystanie surowców i zmniejszenie emisji.
- End-to-End Customer Focussed Engineering, czyli kompleksowa realizacja oczekiwań klientów wobec produktów.
- Stworzenie organizacji skupionej na pracowniku firmy – indywidualne różnice wykorzystywane są na rzecz wzmocnienia organizacji i budowę przyjaznego środowiska pracy.
- Smart Manufacturing – inaczej inteligentna produkcja, która zakłada stosowanie zintegrowanych systemów reagujących w szybki sposób na zmienne warunki.
- Model biznesowy oparty na nowym łańcuchu wartości – to fabryka otwarta na zrozumienie potrzeb wszystkich uczestników procesu.
Jakie są korzyści z wdrożenia Przemysłu 4.0 w firmie?
Czwarta rewolucja przemysłowa wymaga nowego spojrzenia na zachodzące zmiany niezależnie od branży, systemu, czy społeczności. Konieczny jest nowy sposób myślenia, który umożliwi przedsiębiorstwom osiągnięcie odpowiednich wyników finansowych z uwzględnieniem właściwego miejsca człowieka w świecie nowoczesnych technologii.
Wiemy już, co to jest przemysł 4.0, jakie zatem mogą być korzyści w firmie z jego wdrożenia? Przede wszystkim przedsiębiorstwo staje się staje się bardziej konkurencyjne. Inwestycja w technologię i nowoczesne rozwiązania w zdecydowany sposób usprawnia procesy, co daje nową jakość usług klientom. Powoduje również to, że pracownicy są bardziej wydajni i łatwiej rozwiązują potencjalne problemy. Wzmacnia się współpraca między działami, a pełniejsze wykorzystanie danych w czasie rzeczywistym pomaga w podejmowaniu szybszych i lepszych decyzji. Dodatkowymi korzyściami będą:
- wzrost produktywności i automatyzacji – prognozy będą dokładniejsze, zwiększy się terminowość dostaw, plany będą zoptymalizowane pod kątem zysku,
- większa elastyczność w zmiennej sytuacji rynkowej – zaawansowane planowanie pozwala w cyfrowy sposób kształtować łańcuch dostaw,
- możliwość testowania nowych modeli biznesowych – to szansa na obniżenie kosztów i zwiększenie efektywności,
- realizacja celu środowiskowego – pozwala wprowadzić ekologiczne rozwiązania bez utraty zysków.
Obecna zmiana wydaje się jedną z najważniejszych, bo dotyka każdego aspektu naszego życia, czyli pracy, zdrowia i relacji międzyludzkich. Przemysł 4.0 opiera się na inteligentnej, połączonej technologii zarówno wewnątrz organizacji, jak i w codziennym życiu. Większość decyzji przenosi się do kompetencji maszyn, więc zaciera się granica pomiędzy tym, co biologiczne, a tym, co cyfrowe. Przełomowe momenty charakteryzują się również tym, że oprócz wpływu twórczego, mają również wpływ destrukcyjny. Dają nowe możliwości i jednocześnie stanowią ryzyko. Przykładem mogą być zmiany na rynku pracy, które powodują zanik wielu tradycyjnych zawodów.
Zainteresować Cię również może artykuł: Industry 4.0