Czym jest lean manufacturing?
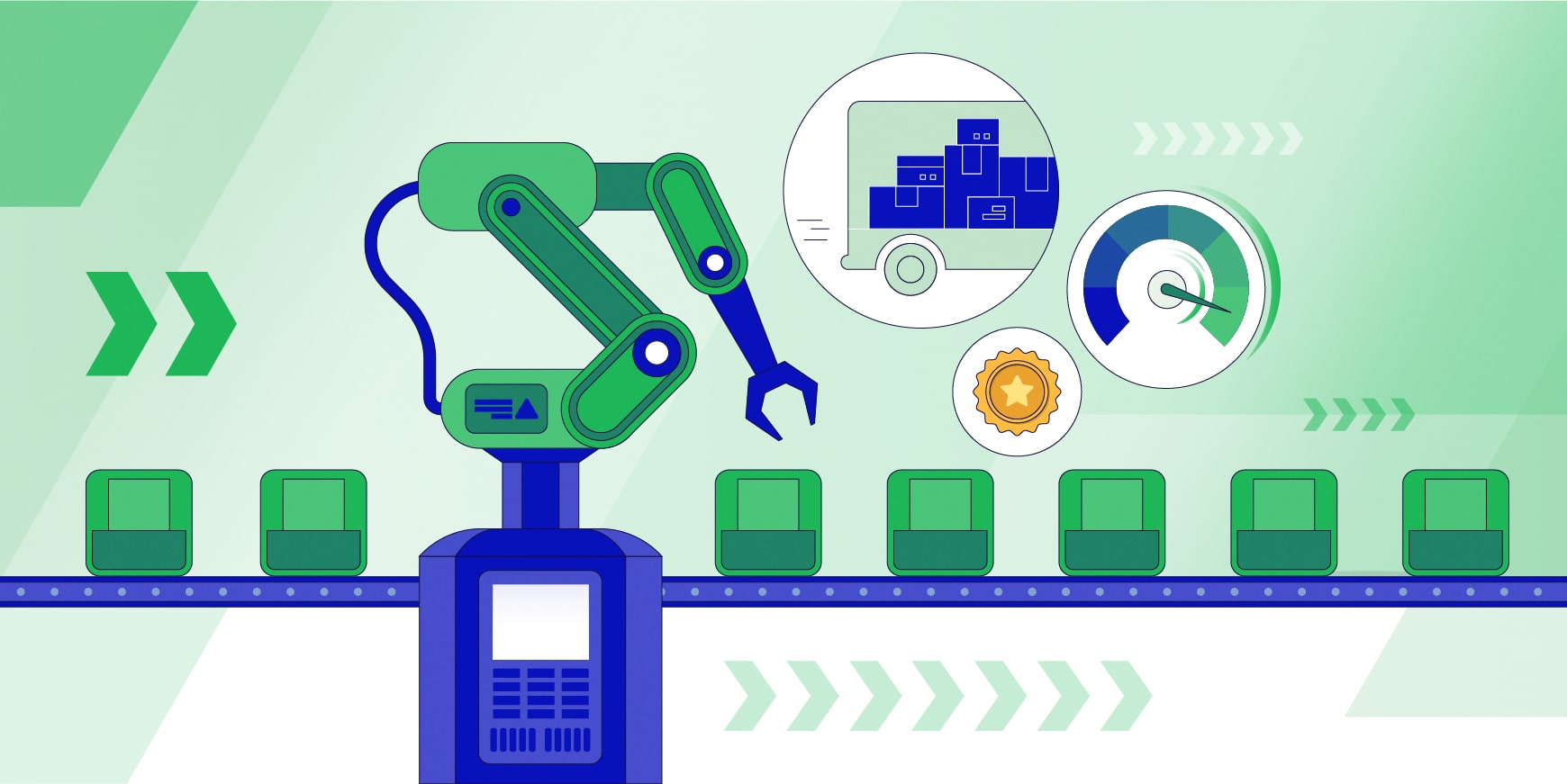
W czasach kiedy wysoka konkurencyjność ma szczególne znaczenie, firma produkcyjna powinna posiadać kluczową umiejętność redukcji kosztów operacyjnych przy jednoczesnym podnoszeniu wydajności. Potrzeba ta doprowadziła do rozwoju wielu nowych koncepcji zarządzania, z których jedną z najbardziej popularnych metod jest Lean Manufacturing, czyli tzw. szczupła produkcja. Co to jest Lean Manufacturing? I jak wpływa na wzrost konkurencyjności przedsiębiorstw produkcyjnych?
Spis treści:
- Lean manufacturing – definicja i filozofia lean
- Historia i główne założenia lean manufacturing
- Narzędzia Lean Manufacturing – przykłady
- Lean Management a Lean Manufacturing – różnice
Lean manufacturing – definicja i filozofia lean
Koncepcja Lean Manufacturing, czyli tzw. szczupłego wytwarzania opiera się na zarządzaniu prowadzącym do poprawy jakości produktów i procesów oraz eliminowania marnotrawstwa. Lean to mniejszy wysiłek ludzi, mniej miejsca w zakładzie, mniej narzędzi, połowa inwestycji i czasu na zaprojektowanie wyrobu produkowanego dwa razy szybciej. Polega na eliminowaniu czynności niepotrzebnych, a czynności niezbędne wykonuje się raz i w odpowiedniej kolejności. Działania zgodne z filozofią lean manufacturing, pozwalają na ograniczenie zużycia wszystkiego, co potrzebne w procesie produkcyjnym. Dzięki temu otrzymujemy produkt lepiej dopasowany do potrzeb klientów i dodatkowo wytworzony po dużo niższych kosztach w porównaniu do produkcji masowej. Koncepcja lean manufacturing polega więc na usprawnieniu działania systemu produkcyjnego poprzez likwidację wszelkiego rodzaju marnotrawstwa, aby produkować dokładnie tyle, ile potrzebują klienci. Każdy niesprzedany produkt traktowany jest jako strata.
Historia i główne założenia lean manufacturing
Mimo tego, że elementy szczupłej produkcji stosowane były już w XVI wieku to koncern motoryzacyjny Toyota uznawany jest za prekursora koncepcji Lean Manufacturing. W latach 40. XX wieku japoński inżynier Taiichi Ohno rozpoczął szereg zmian z zakresu organizacji produkcji. Działania te przekształciły Toyotę z lokalnej fabryki w światowego lidera branży motoryzacyjnej. Wprowadzony system produkcyjny stał się alternatywą dla modelu produkcji masowej. Ciekawostką jest to, że zastosowane narzędzia i techniki zostały odkryte i opisane stosunkowo późno, bo dopiero w latach 80. XX wieku, kiedy w Stanach Zjednoczonych zaczął nasilać się kryzys motoryzacyjny spowodowany rosnącą konkurencyjnością japońskich producentów. Efektem badania przyczyn kryzysu była opublikowana w 1990 roku książka „Maszyna, która zmieniła świat”, w której po raz pierwszy opisano koncepcję Lean Manufacturing.
Najczęściej stosowaną formą graficzną, która przedstawia podsumowanie najważniejszych założeń szczupłej produkcji, jest tzw. dom systemu produkcyjnego Toyoty (TPS – Toyota Production System).
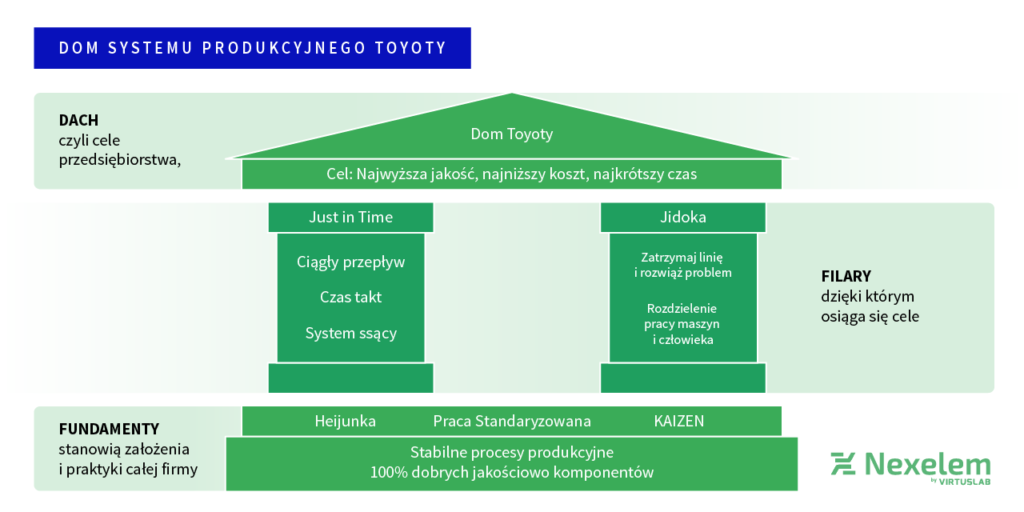
Rys. Dom systemu produkcyjnego Toyoty. Źródło: Ingaldi i Klimecka-Tatar, 2015, str. 114.
Dom TPS składa się z takich elementów, jak:
- dach, czyli cele przedsiębiorstwa,
- filary, dzięki którym osiąga się cele,
- fundamenty, które stanowią założenia i praktyki całej firmy.
W ujęciu najprostszym zakłada się, że aby zrealizować cel (w tym przypadku dach), należy zacząć od budowy solidnych fundamentów, na których można oprzeć odpowiednie filary. Przyjmuje się również, że nieprawidłowe funkcjonowanie dowolnego elementu w systemie osłabia całą konstrukcję.
Obecnie definicja Lean Manufacturing wykracza poza zakres systemu produkcyjnego Toyoty, dzięki czemu można dostosować ją do przedsiębiorstw o innej specyfice funkcjonowania. Lean to aktualnie bardziej uniwersalny model opisywany w trzech kategoriach:
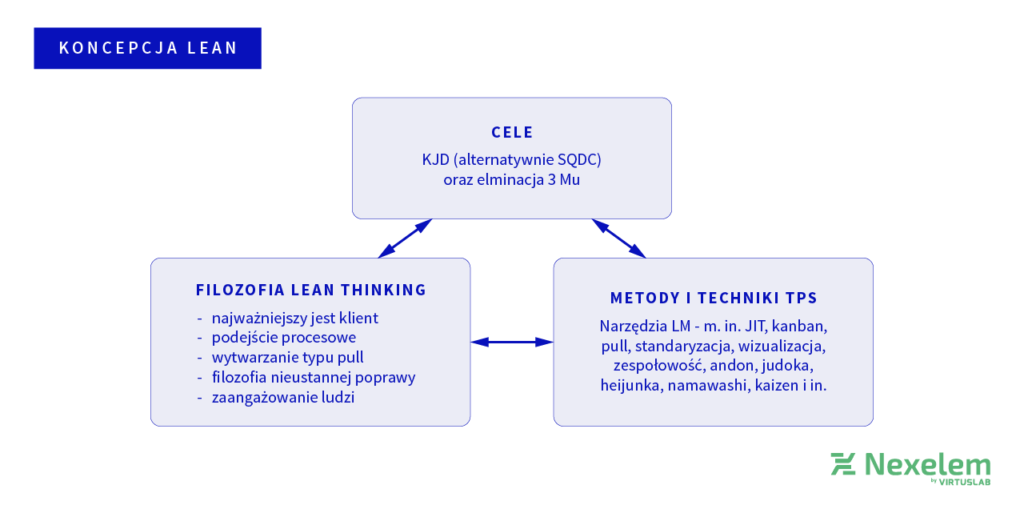
Rys. Istota koncepcji lean. Źródło: Walentynowicz, 2013, str. 56.
Cele koncepcji Lean manufacturing
KJD to skrót określający główne cele Lean Manufacturing:
- K (koszty) – redukcja kosztów,
- J (jakość) – poprawa jakości wytwarzanych produktów,
- D (dostawy) – skrócenie czasu od zamówienia do dostarczenia klientowi.
W języku angielskim określane są za pomocą SQDC (Security, Quality, Delivery, Cost), gdzie cele te zostały rozszerzone o aspekt zachowania bezpieczeństwa w pracy.
Przedsiębiorstwa zgodne z filozofią lean dążą również do eliminacji tzw. 3 Mu, czuli Mura (nierytmiczność), Muri (przeciążenie w pracy) i Muda (marnotrawstwo). Czynniki te są ze sobą powiązane, co może stanowić liczne problemy w przedsiębiorstwie. Przykładowo nierytmiczność dostaw od dostawców, czy zmienność w planach produkcji, może powodować nieefektywne wykorzystanie zasobów ludzkich i maszyn, które mogą stać niewykorzystane lub pracować w zbyt dużym tempie. Nadmierne przeciążenie prowadzi do spadków jakości i większej ilości błędów. W kontekście Lean Manufacturing najwięcej uwagi skupia się na Muda, czyli marnotrawstwu, które bardzo często jest widoczne w procesach produkcyjnych. Aktualnie wyróżnia się jego 8 podstawowych rodzajów, z czego Taiichi Ohno określił pierwszych 7. Są to:
- Nadprodukcja – kiedy ilość wytwarzanych dóbr lub usług przekracza zapotrzebowanie klientów. Sytuacja ta jest aktualnie przedstawiana jako największy rodzaj marnotrawstwa.
- Braki produkcyjne – produkt nie spełnia wymagań klienta, więc konieczne są poprawki lub złomowania części.
- Zbędne zapasy – czyli przechowywanie zbyt dużej ilości materiałów w firmie, tj. materiały surowe, półprodukty, części zamienne. W biurze to: nadmierna ilość otrzymywanych maili, wydrukowanych dokumentów, materiałów biurowych.
- Oczekiwanie – spowodowane brakami materiałów, niedziałającym systemem komputerowym, awariami, przezbrojeniem maszyn.
- Zbędne przetwarzanie – skupienie uwagi na czynnościach, które nie podnoszą wartości produktu, np. nadmierna obróbka części.
- Transport – dotyczy odległości, jakie produkty, półprodukty lub narzędzia pokonują pomiędzy np. magazynem a stanowiskiem roboczym.
- Zbędny ruch – do realizacji zadania konieczne jest wykonanie zbędnych ruchów.
- Stracona kreatywność pracowników – to sytuacja, w której ignorowane są pomysły członków organizacji. Powtarzalność zadań powoduje, że pracownik staje się ekspertem w danej dziedzinie, co należy wykorzystywać do doskonalenia realizowanych procesów.
Metody i techniki TPS
Lean Manufacturing dostarcza nam aktualnie bardzo rozbudowany system narzędzi, których celem jest wyeliminowanie 3 Mu, czyli marnotrawstwa, nierytmiczności oraz przeciążenia pracowników. Część metod pochodzi z Systemu Produkcyjnego Toyoty, które dodatkowo wraz z popularyzacją koncepcji lean, zostały poszerzone o dodatkowe techniki.
Klasyfikacja narzędzi została zdefiniowana przez M. Ćwiklińskiego i H. Obrę, którzy wprowadzili podział na te, które służą:
- doskonaleniu organizacji, np.: JIT (Just In Time), Wewnętrzny system ssący/ supermarkety system Kanban, One Piece Flow (przepływ jednej sztuki), 5S, TPM, Standaryzacja pracy, Poziomowanie produkcji (heijunka), Jidoka, Samokontrola na stanowisku pracy, Praca zespołowa, System uzgadniania decyzji Nemawshi, Kaizen, Hoshin kanri.
- rozwiązywaniu problemów, np.: Andon, Poka Yoke, Rozwiązywanie problemów w miejscu ich powstania (Genchi Genbutsu), Burza mózgów, PDCA, Wykresy Pareto, Wykres Ishikawy, 5 razy Dlaczego.
Należy jednak pamiętać, że samo stosowanie narzędzi tzw. szczupłej produkcji nie spowoduje, że firma będzie działać zgodnie z tą koncepcją. Konieczne jest dokonanie głębszych zmian poprzez wdrożenie filozofii Lean Thinking.
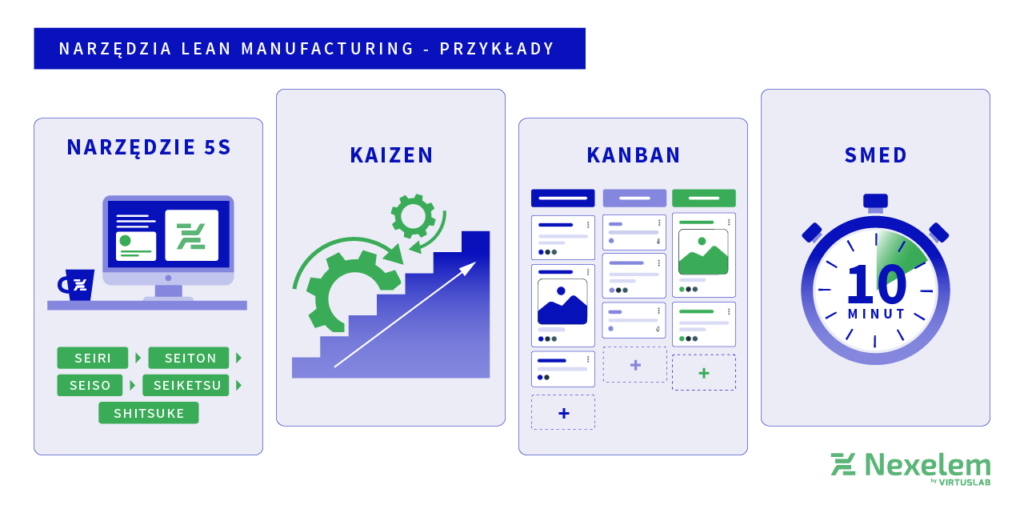
Narzędzia Lean Manufacturing – przykłady
Narzędzie 5S – służy do stworzenia optymalnego miejsca pracy poprzez:
- Seiri (selekcja, sortowanie), polega na identyfikacji i usunięciu wszystkich przedmiotów zbędnych na stanowisku pracy.
- Seiton (systematyka, uporządkowanie), wyznaczenie miejsc dla wszystkich przedmiotów, aby ograniczyć zbędny ruch i wysiłek.
- Seiso (sprzątanie), utrzymanie stanowisk pracy w czystości poprzez określenie kto i kiedy, co ma zrobić.
- Seiketsu (standaryzacja), opracowanie i wdrożenie dla pierwszych trzech kroków 5S, powinny być proste i wizualne.
- Shitsuke (samodyscyplina, samodoskonalenie), utrzymanie wprowadzonych usprawnień na stanowisku pracy poprzez stałe promowanie 5S w miejscu pracy, komunikowanie wyników oraz szkolenia pracowników.
Kaizen – to nieustanne doskonalenie się poprzez ciągłe wprowadzanie zmian i usprawnień za pomocą małych kroków. Celem jest skrócenie czasu realizacji procesu oraz poprawa jakości. Regułą jest zaangażowanie pracowników na wszystkich szczeblach. Proces myślowy zachodzi na każdym etapie produkcji, czyli jest odpowiedzią na tradycyjne podejście do produkcji masowej. Dąży do redukcji kosztów i poprawy ergonomii stanowisk roboczych.
Kanban – w języku japońskim oznacza tablicę wizualną. Metoda ta polega na sterowaniu produkcją przez zdarzenia, które następują bezpośrednio na produkcji. Korzyścią narzędzia jest: krótki czas przetwarzania, niskie zapasy, terminowość realizacji, a także kontrola jakości na wszystkich etapach produkcji.
SMED – wyznacza cel, którym jest skrócenie czasu przezbrojenia maszyny do maksymalnie 10 minut.
Cechy charakterystyczne filozofii Lean Thinking
Kluczowym elementem Lean Manufacturing jest filozofia Lean Thinking. Według niej eliminacja marnotrawstwa nie jest celem samym w sobie, a wyznaczeniem drogi, po której przedsiębiorstwo powinno się poruszać. W myśleniu tym nie chodzi o wdrażanie kolejnych metod i narzędzi, kluczowe jest dążenie do doskonałości poprzez kreowanie odpowiednich postaw wśród pracowników. Zasady te przedstawiono w formie pięcioetapowego procesu:
- Określenie wartości – polega na prawidłowym zdefiniowaniu wszystkich czynności wykonywanych przez firmę, za które klient jest gotów zapłacić. Eliminuje się te, które nie dodają wartości, czyli stanowią element marnotrawstwa.
- Identyfikacja strumienia wartości – poziomy przepływ materiałów i informacji przez wszystkie komórki przedsiębiorstwa, czyli od zamówienia do dostarczenia produktu, powinien być kontrolowany pod kątem tego, aby każda wykonywana czynność w konkretnym dziale dodawała wartość.
- Stworzenie przepływu – czyli optymalizacja czynności prowadząca do uzyskania stabilnego przepływu. Eliminuje się przestoje, czas oczekiwania pomiędzy procesami, ewentualne zakłócenia.
- Wprowadzenie systemu ssącego – system ssący, czyli pull ma powiązać proces wytwarzania produktu ze zgłaszanym popytem, aby procesy wytwórcze odbywały się w dostosowanym tempie i w wymaganych ilościach.
- Dążenie do perfekcji – zakłada, że proces doskonalenia się firmy jest stały, dzięki temu mamy coraz wyższą jakość oraz niższe koszty i krótszy czas dostawy.
Poza metodami i narzędziami, które służą do zarządzania produkcją, Toyota położyła duży nacisk na rozwijanie kultury organizacyjnej. Budowanie wartości i odpowiednich postaw wśród pracowników to coś, co odróżniało tę japońską firmę od konkurencji, która wprowadzała system produkcji Toyoty. Przewaga Lean Manufacturing nad innymi stylami zarządzania nie wyróżniała się zbiorem narzędzi, a specyficzną filozofią myślenia i działania.
Lean Management a Lean Manufacturing – różnice
Choć terminy te brzmią podobnie to jednak odnoszą się do innych obszarów funkcjonowania przedsiębiorstwa. To, co odróżnia te dwie koncepcje to zakres podejmowanych działań. Lean Management jest koncepcją szerszą i polega na usprawnianiu funkcjonowania przedsiębiorstwa we wszystkich jego obszarach, czyli od produkcji, przez pracę działu handlowego, po księgowość i controlling. Zakłada, że przedsiębiorstwo działa prawidłowo wtedy, kiedy dba się o harmonijne działanie wszystkich tych elementów. Celem Lean Manufacturing jest również stały rozwój i usprawnianie prowadzonej działalności, jednak zakres tej koncepcji jest znacznie węższy. Skupia się przede wszystkim na aktywności działów operacyjnych (produkcyjnych), a inne obszary takie jak księgowość, zaopatrzenie schodzą na drugi plan.
Należy pamiętać, że sprawne zarządzanie produkcją to aktualnie podstawa redukcji kosztów w przedsiębiorstwie produkcyjnym. Odpowiedni system pozwala planować produkcję wieloetapowo, jednocześnie zapewniając jej monitorowanie w czasie rzeczywistym.
Więcej na ten temat w artykule: Efektywne zarządzanie produkcją. Elementy procesu, metody i korzyści z wdrożenia systemu.