Examples of Change Management
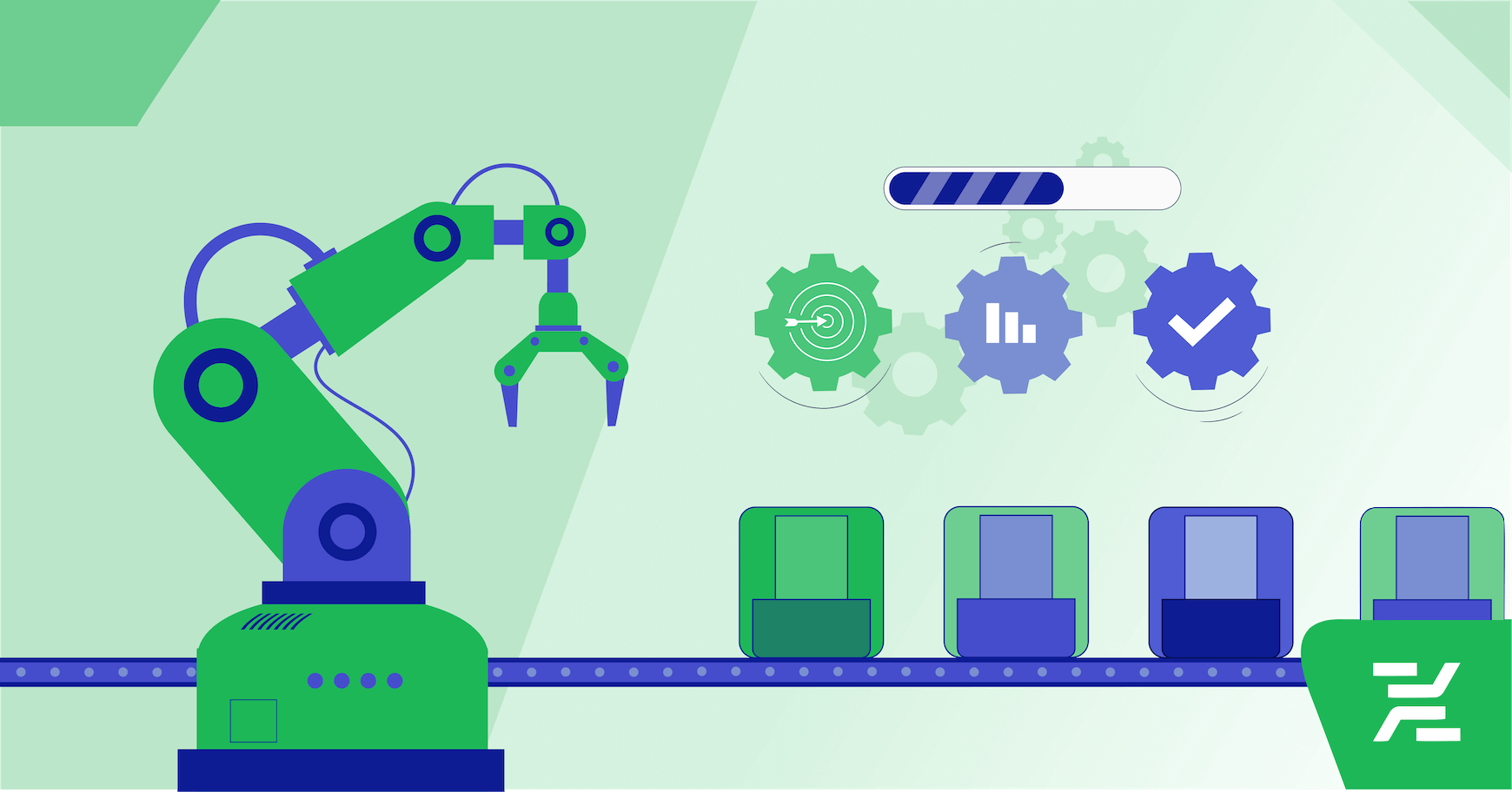
Change is often met with resistance among people, especially in complex systems such as those related to manufacturing. Hence, the concept of change management is proving to be particularly relevant in today’s highly turbulent economic reality. Therefore, let’s examine examples of this approach in the context of manufacturing companies.
Table of contents:
- What is Change Management?
- Stages of Change Management
- Examples of Change Management in Manufacturing Organizations
- Examples and Models of Change in Manufacturing Companies – Presentation
- Model of the Power Triangle Concept PPT in Change Management
- Kurt Lewin’s Model of Change
- Steps of Change According to Kotter
- Tactics for Dealing with Resistance, According to Schlesinger
What is Change Management?
The term “change management” actually refers to a multi-step process, the premise of which is to implement modifications and maintain them. The primary goal of such improvements is to enhance the company’s competitiveness and profitability, particularly through changes to the production process.
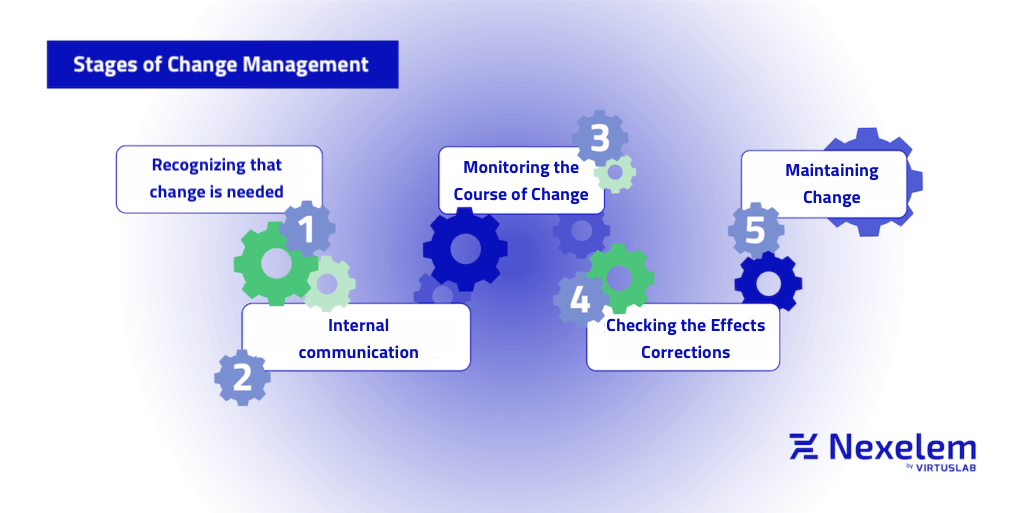
Stages of Change Management
For this to be possible, change management must have appropriate stages, among which the most common are:
1. Recognizing that change is needed
This requires data and observations that can be collected through appropriate technological solutions.
2. Internal (and often external) communication
As we mentioned, change often provokes resistance among people who are more comfortable with the status quo. That is why it is so important to indicate how beneficial it will be to the processes and, of course, most importantly, to the people involved.
3. Monitoring the Course of Change
Any management process must involve monitoring. Otherwise, we are unable to assess whether the modification is beneficial. The method of monitoring must be envisioned even before the change is implemented.
4. Checking the Effects and Possible Corrections
Modifications are often also required in the change management process. Stubbornly sticking to one’s assumptions, even if the change appears not to be beneficial at first glance, can result in financial losses and erode trust among employees.
5. Maintaining Change
It is not uncommon for systems to revert to their original state if they are not maintained in their new setting for an extended period of time. That’s why it’s so important to understand what change management entails, including its stages and the role employees play in it.
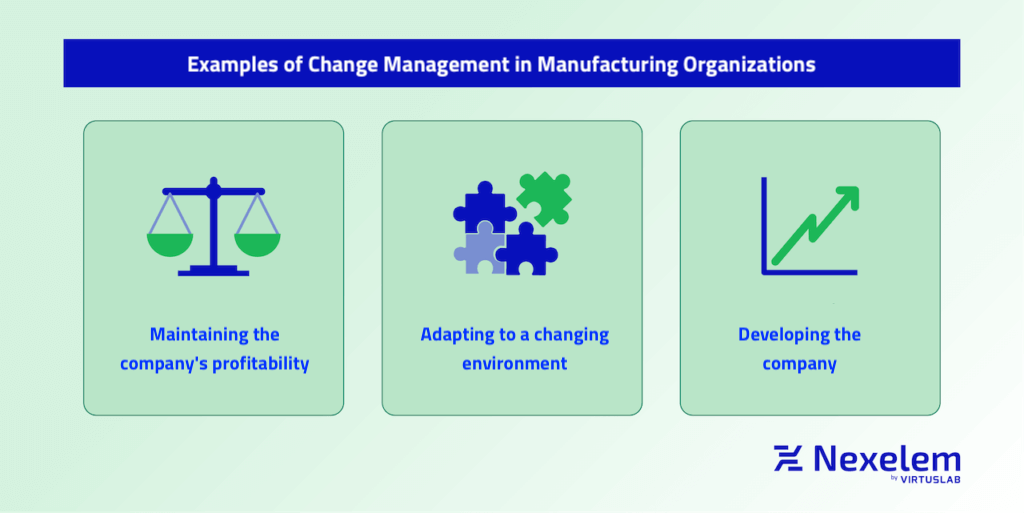
Examples of Change Management in Manufacturing Organizations
The reality in manufacturing companies is virtually never stable and one-dimensional. These companies are constantly dealing with changes, such as fluctuations in the cost of raw materials and their availability, as well as those related to employee turnover, for example. All of this with the simultaneous overarching goal of keeping the company profitable and ultimately also growing.
Hence, the change for such entities is, first and foremost, the continuous optimization of various processes through the use of appropriate technological solutions. However, to identify areas that need modification, it is essential to continually monitor the production status. This is because the basis for change is concrete data, the collection of which requires minimal effort. This is because modern systems, based on digital or analog sensors that analyze various aspects of the production process, including, most importantly, its speed, can be helpful. Thus, information is obtained on production efficiency and any critical points, as well as whether the whole is aligned with the objectives.
If, on the other hand, the indicators deviate from the optimum, then changes are necessary. They may involve, for example, implementing a modern MES system to manage production, providing additional training for employees, or a comprehensive reorganization of the production cycle to improve its efficiency. An example of modification is also upgrading the machinery to a more efficient fleet.
As you can see, managing change requires the right approach to push it through and to sustain it. The process can be demanding, although the modifications themselves are not to be feared. After all, in today’s rapidly changing economic landscape, stagnation is a way to fail quickly and be overtaken by market competitors.
Examples and Models of Change in Manufacturing Companies – Presentation.
Recently, the Nexelem team participated in an extraordinary event – the “Factory of the Future” conference. Our attention was drawn to a fascinating presentation by Marcin Wojcieszek on the topic of change management. A topic so close to our heart because almost every correct implementation of an IT system for production management involves some changes in the client’s organization. All the more reason why Marcin’s lecture as head of the production facility caught our attention.
He is the director of the Lamintex factory in Nowy Sącz. He has been involved with Lean philosophy and tools for years. He began his professional adventure in 2006 in the automotive industry, where he developed his management skills over the years. He has successfully implemented and developed teams towards Lean Management, Lean Manufacturing, and Leadership.
Marcin says that the key to successful change is people, and his motto is “Always with the people and for the people, because the quality of an organization will never be better than the quality of the minds that create it.”
Model of the Power Triangle Concept PPT in Change Management.
Marcin, could you explain the concept of the Triangle of Power in more detail?
Marcin: Of course.
– The power triangle is the key to sustainable change, P+P+T=P in that order, where P is people, P is processes, T is technology, and P is power.
– People always come first and are at the top of the triangle. With people, we build a Lean culture and a team based on Leadership. If we have P+P, we start to affect T (technology) using Lean tools. If we implement sustainable standards of conduct based on effective tools, then processes will begin to improve, positively impacting the entire organization.
– Seemingly simple, but at the same time difficult, because every action causes reactions, hence the “saw” between PPT. The role of Leaders is to smooth the chart as much as possible and keep it as it is. Then we will ensure that the changes are sustainable and T will continue to improve. If we initiate the change through processes, regardless of the tools we use, and overlook P+T, the change will be sporadic, and the process will improve temporarily.
– However, it is essential to remember that with change also comes resistance.
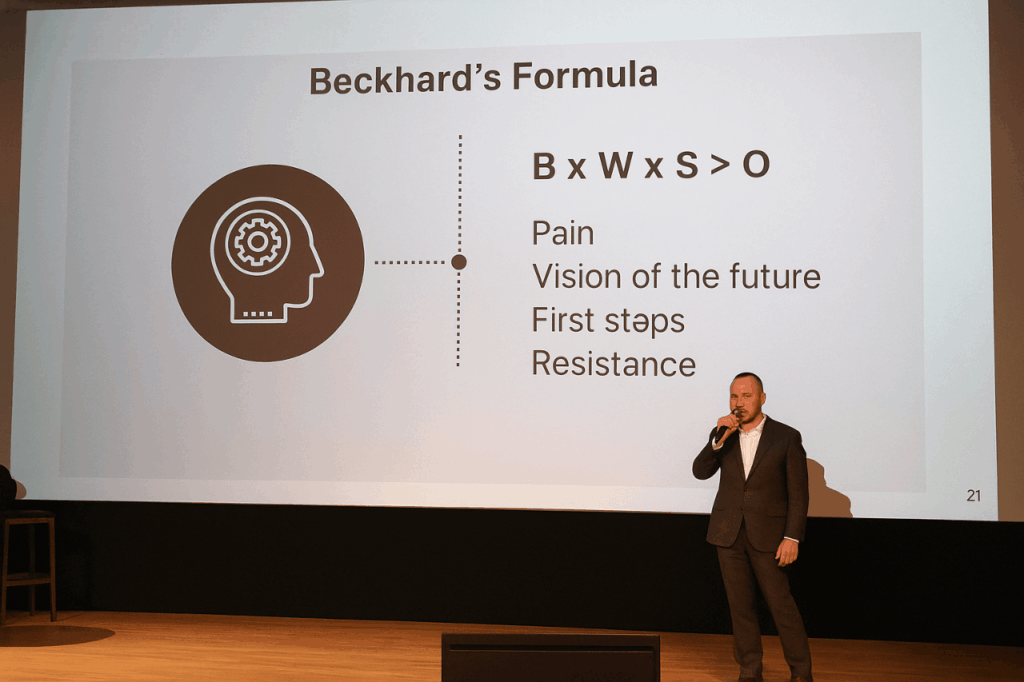
Formuła Beckharda
Kurt Lewin’s Model of Change
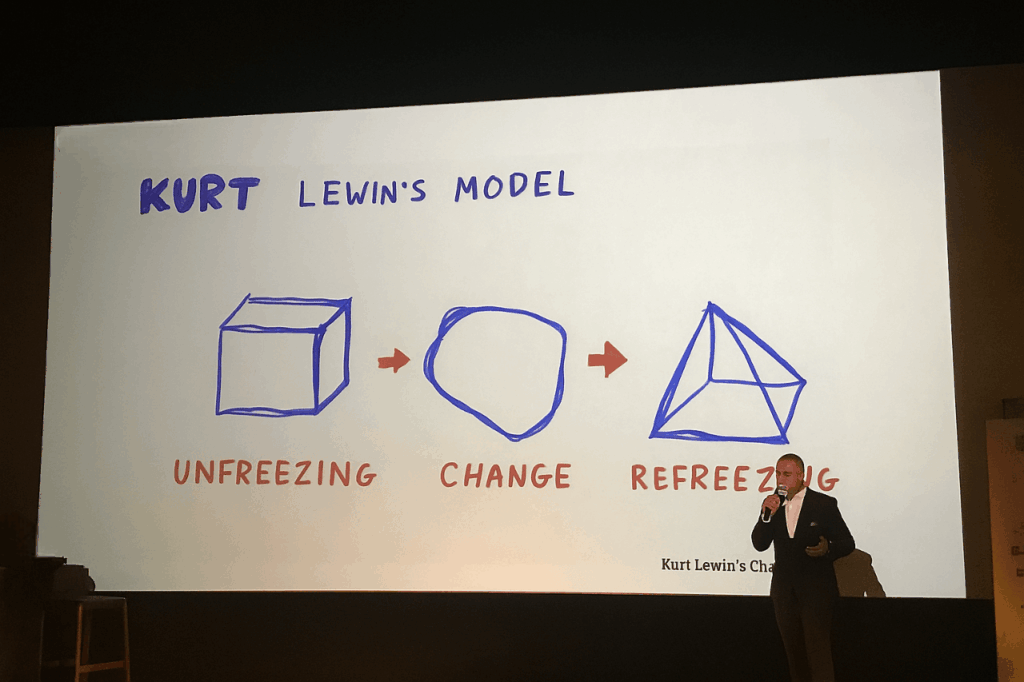
Model of change according to Kurt Lewin: Unfreeze, Change, and Refreeze.
Steps of change according to Kotter
- Raise awareness of the urgency of change
- Creating a change leadership team
- Creating the right vision and strategy
- Reliable communication
- Empowerment to take action
- Small but quick success
- Not giving up
- Freezing the changes
The steps of change, according to Kotter, can be seen as a detailed elaboration of Lewin’s model.
Tactics for dealing with resistance, according to Schlesinger
- Communication
- Participation
- Facilitation and support
- Negotiations
- Co-option
Manipulation and coercion are obviously examples of bad tactics.
Courtesy of Marcin, we can now make his presentation available to a broader audience.
What elements should not be changed in the production organization at such an uncertain economic moment for production? Who should be the ambassadors of change, and how can they effectively lead transformation projects to achieve ongoing KPIs and OEE?