MRP System – Why does a manufacturing company need material requirements planning software?
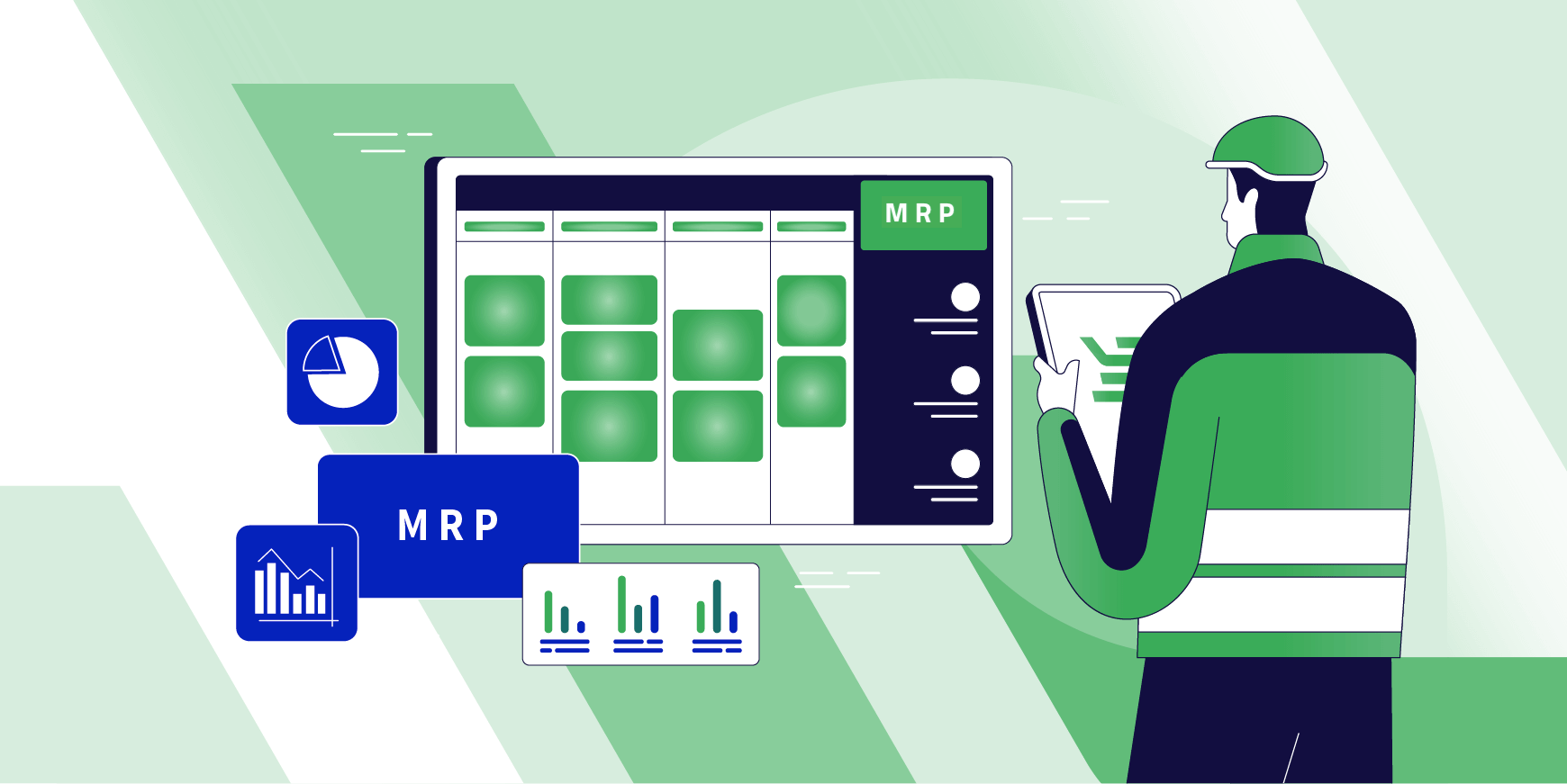
The MRP (Material Requirements Planning) system is an advanced software tool that assists manufacturing companies in efficiently managing their production processes. The first MRP systems emerged in the 1960s, and since then, they have evolved significantly, becoming an essential element of modern industrial operations. The primary goal of an MRP system is to accurately plan the requirements for raw materials, components, and parts, which translates into optimising production costs, shortening lead times, and improving overall organisational efficiency.
Table of Contents:
- Key Functions of the MRP System
- How Does an MRP System Work?
- Why Should You Implement an MRP System in Your Company?
- How to Implement an MRP System Properly?
- Integrating with an MRP System – What Are the Options?
- MRP System: Summary and Conclusions
Key Functions of the MRP System
The core functions of the MRP system include
- Planning material requirements based on the production schedule, the Bill of Materials (BOM), and inventory levels.
- Generating production and purchase orders, taking delivery schedules into account.
- Monitoring and controlling the execution of individual stages of the manufacturing process.
- Optimising stock levels by maintaining an optimal amount of raw materials and semi-finished products.
- Integrating data from various areas of the company, such as sales, logistics, and finance.
With these functionalities, the MRP system provides comprehensive support for manufacturing companies, managing the entire product lifecycle—from planning and production to delivery to the customer.
How Does an MRP System Work?
The operation of an MRP system is based on three key data sources:
- Master Production Schedule (MPS) – contains information about planned production dates and quantities of finished goods.
- Bill of Materials (BOM) – specifies the list of materials and components needed to produce a particular product, along with their quantities.
- Inventory Levels – information about the current stock of raw materials, semi-finished products, and finished goods.
Based on this data, the MRP system generates a production plan for each component, considering the required quantities of materials and production order deadlines. Simultaneously, it creates a procurement plan, determining the dates and quantities of raw material orders.
Planning in the MRP system can occur in two directions:
- Forward Planning – starts from the production schedule of finished goods and determines the deadlines for component orders accordingly.
- Backward Planning – begins with the availability of raw materials and components, then sets the deadlines for producing finished goods to ensure timely delivery to the customer.
The choice of planning method depends on the specific industry and market conditions in which the company operates.
Benefits – Why Should You Implement an MRP System in Your Company?
Implementing an MRP system provides manufacturing companies with several tangible benefits, including:
- Reduction of production costs through inventory optimisation and the elimination of downtime.
- Shorter lead times thanks to better planning and synchronisation of deliveries.
- Improved product quality resulting from better control over the manufacturing process.
- Increased production flexibility in response to changing market demands.
- Better communication and information flow between company departments.
- Support for decision-making based on reliable data.
It is important to note that the MRP system serves as the foundation for many advanced software solutions, such as:
- MRP II (Manufacturing Resource Planning) – an expanded system for planning manufacturing resources.
- ERP (Enterprise Resource Planning) – a system for managing enterprise resources.
- APS (Advanced Planning and Scheduling) – a production scheduling system.
Leveraging the functionalities of the MRP system opens up opportunities to gradually expand IT systems, adapting them to the changing needs and growing complexity of production processes as the company develops.
How to Implement an MRP System Properly?
Implementing an MRP system is a complex process that requires careful planning and a well-thought-out strategy. Several crucial factors must be considered to ensure that the implementation is successful.
Set Clear Goals
The first step in implementing an MRP system is to precisely define the goals that the organisation wants to achieve. These goals should be specific, measurable, and realistic – aligned with the SMART methodology. For example, Company X might aim to increase production efficiency, reduce inventory levels, or improve on-time delivery. Clearly defined goals will allow Company X to better focus its implementation efforts based on the expected outcome and facilitate the assessment of project progress.
Choose the Right Software
The choice of the appropriate system should be based on the specific industry in which the company operates and its individual needs. Two main criteria to consider are the flexibility and scalability of the chosen solution. Such characteristics will allow the system to adapt to changing market conditions and the company’s growth.
Let’s Talk about your production
Contact us to discuss a tailored MRP system that takes into account the specifics of your manufacturing company and the industry in which you operate. We’ll show you why our approach to MRP is a real-time solution. Our system “lives on forecasts,” ensuring that you always have access to up-to-date data.
Prepare Organisationally
Implementing an MRP system requires proper organisational preparation. It is essential to analyse existing business processes and identify areas that may need changes. Roles and responsibilities of employees in the context of the new system should also be defined. Preparing the organisation for implementation should include adequate communication – all employees should be fully aware of the upcoming changes and their impact on daily work.
Engage a Competent Team
Without a well-organised implementation team with the right skills, the process cannot move forward! The team should include both IT specialists and representatives from various departments who understand the production processes. Collaboration between departments is crucial to understanding the needs and expectations of all system users. The team should also be responsible for monitoring the progress of the implementation and making any necessary adjustments to the action plan.
Train Employees
Users must be properly trained to efficiently operate the new system and utilise its full capabilities. Training should be tailored to the different skill levels of participants and their roles within the organisation. It’s best to conduct training in small groups to allow team members to interact with the system and practice. Preparing user manuals is also valuable, providing a significant aid for new employees joining the team after the implementation process is complete.
We Can Help You
Our system is highly intuitive and easy to use, even for non-technical users. Unlike solutions that have been on the market for decades, Nexelem was designed in collaboration with the industry, and we focused on making our production management system enjoyable and helpful in everyday work. If you have any questions about implementing Nexelem in your company, click the button below and reach out to us.
Monitor Progress
The system has been successfully implemented, and employees now know how to use it? Excellent – but remember, the process does not end here. Monitoring the MRP system’s performance and evaluating the results against the previously set goals is essential. Regular analyses help identify any issues and areas that may require further optimisation. Collecting feedback from system users is also valuable – feedback helps tailor the system’s functionality to the organisation’s needs.
Don’t Forget About Change Management and Continuous Improvement
Implementing an MRP system involves introducing changes to business processes and organisational culture. To help employees adapt effectively to the new conditions, a change management strategy is necessary. A company that has implemented an MRP system should also strive for continuous improvement of its processes and systems. Regular software updates, employee training, and introducing new functionalities can contribute to further increasing production efficiency and improving customer service quality.
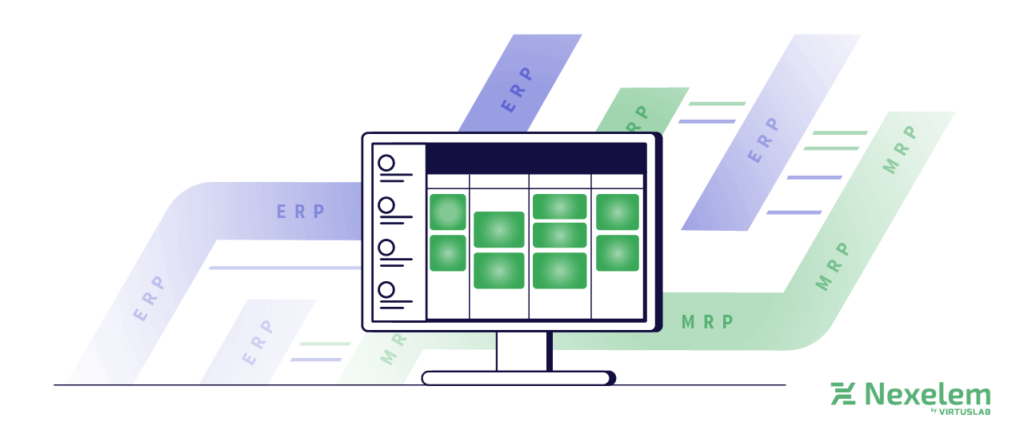
Integrating with an MRP System – What Are the Options?
MRP is not ERP. As mentioned above, the MRP system is a critical element of many advanced IT solutions used in production management. However, the ability to integrate with other key systems in the manufacturing enterprise, such as ERP or MES, is equally important to create a comprehensive environment for managing production and logistics, ensuring smooth information flow and process optimisation.
MRP and MES
The MES system is responsible for executing production orders generated by MRP. This integration allows for the automatic transfer of data on the status of orders from MES to MRP, enabling real-time monitoring of production progress. The automatic generation of production documents and real-time data analysis means that the company can respond more quickly to problems and make decisions based on reliable information.
MRP and WMS
Integrating MRP with a warehouse management system (WMS) ensures efficient supply chain management. The integration allows for the automatic generation of picking orders based on production plans from MRP, which enables the monitoring of inventory levels and automatic replenishment of stock, translating into optimised warehouse processes, from receipt to dispatch.
MRP and Logistics Systems
Integrating the MRP system with logistics systems is another step towards process optimisation. The possibilities are numerous, and the outcomes can be highly positive. Automatically generating transport orders based on MRP shipping plans to improve timeliness, optimise transport routes and schedules, resulting in increased efficiency of the entire supply chain. Monitoring delivery status and automatically notifying customers about order progress also leads to better customer service.
MRP System: Summary and Conclusions
The MRP system is an extremely powerful tool that enables manufacturing companies to efficiently manage their production processes and achieve measurable business benefits. By precisely planning material requirements, synchronising deliveries, and improving production control, businesses can significantly enhance their competitiveness in the market.
However, implementing an MRP system is a complex undertaking that requires the involvement of management, a competent implementation team, and continuous improvement. Therefore, companies that choose to implement this tool should treat it as a strategic investment in the development and growth of the organisation.
The investment and effort will undoubtedly pay off – the MRP system is an essential element of a modern production facility, allowing for the optimisation of manufacturing processes, cost reduction, and product quality improvement. It’s a must-have for your company too!