Industry 4.0 – What, why, examples?
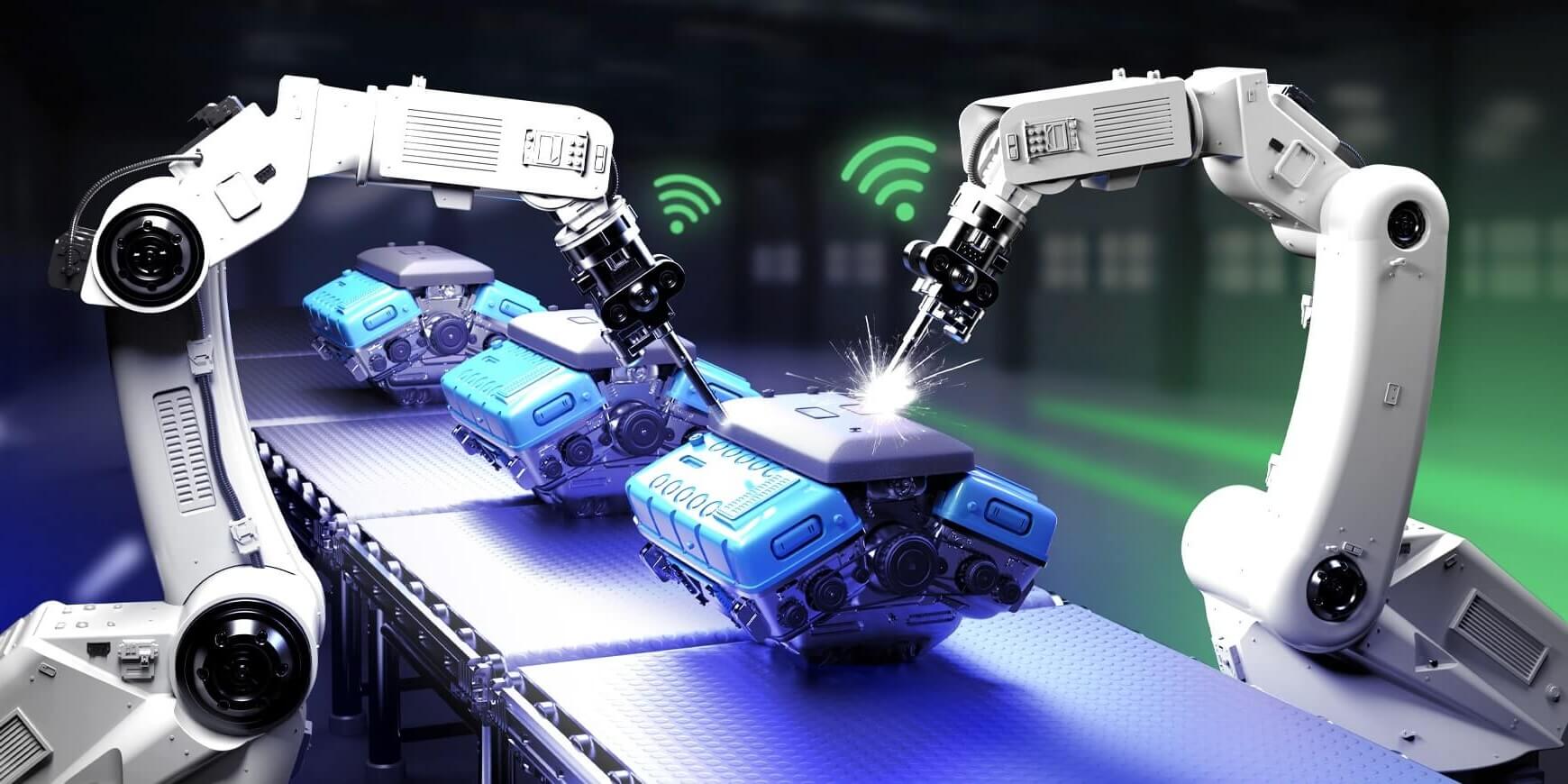
A defining feature of the industrial revolution is the creation of groundbreaking technology that redefines production methods and workflows. The previous three were associated with the invention of the steam engine, the production line, and the computer. We are currently in the midst of the fourth industrial revolution, also known as Industry 4.0. This term describes the social, industrial, and technological changes brought about by the digital transformation of industry. It gives rise to new automation and supply chain monitoring forms through intelligent technologies. Explore what Industry 4.0 is all about.
Table of content:
- The Industrial Revolution – Historical Context of Industry 4.0
- Industry 4.0 – what is it?
- Examples of Industry 4.0 applications
- What are the benefits of implementing Industry 4.0 in a company?
The Industrial Revolution – Historical Context of Industry 4.0
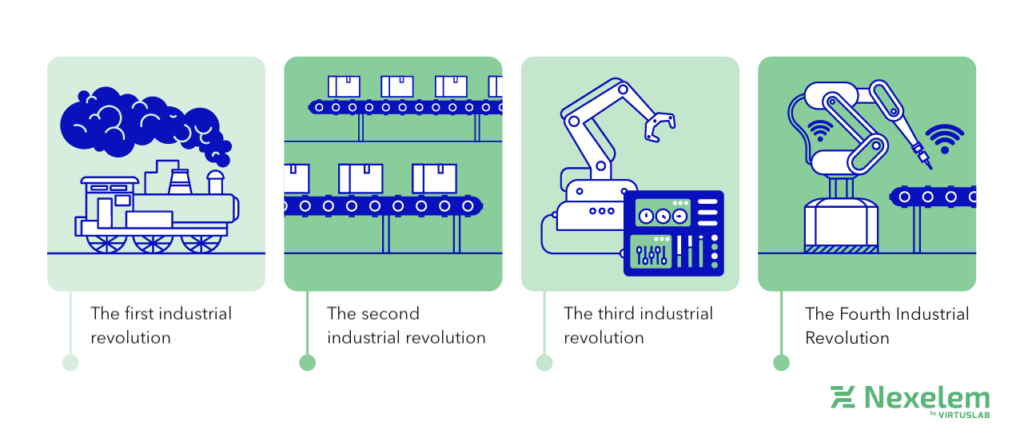
The term revolution defines rapid and radical change. Historically, it has occurred when new technologies, combined with a new way of looking at the world, have caused a profound change in economic systems and social structures.
- The first industrial revolution lasted from 1760 to 1840. It began with the invention of the steam engine, which led to the construction of railways and the introduction of mechanical production. Thread, which had previously been woven by hand on looms, could now be produced eight times faster thanks to mechanisation and the use of steam engines. The use of steam for industrial purposes was the greatest breakthrough in the history of human production. The following years saw the invention of the steam engine and the steam locomotive, which made it possible to transport goods over long distances in much less time. All this contributed to an even more dynamic development of civilisation.
- The second industrial revolution began at the turn of the 20th century with the invention of electricity and the assembly line, which made mass production possible. The first assembly line using electricity was built in 1870. Henry Ford took the idea of mass production and reorganised the way cars were assembled, radically changing the industry. Previously, a car was assembled at a single station, but from then on it was produced in stages on a conveyor belt. The result was a much faster process and a reduction in costs. In the following years, Thomas Edison perfected the alternator and patented the electric light bulb, bringing light into homes.
- The third industrial revolution started in the 1960s. It was triggered by the advent of semiconductors and large computer systems (1960s), personal computers (1970s-80s) and the Internet (1990s). The introduction of programmable logic controllers and computers made it possible to automate the entire production process. From then on, it could take place without human intervention. An example of the application of this approach is the use of robots which, once a sequence of actions has been programmed, carry out tasks without human intervention.
- The Fourth Industrial Revolution is now underway. It builds on the previous ones. It is based on the addition of network connections to computerised production systems, using industrial information and communication technologies. This makes it possible to communicate with other equipment and to transfer information about the equipment itself. The interconnection of all systems leads to intelligent factories in which components of production systems and people communicate via networks. Production thus becomes almost autonomous.
Industry 4.0 – what is it?
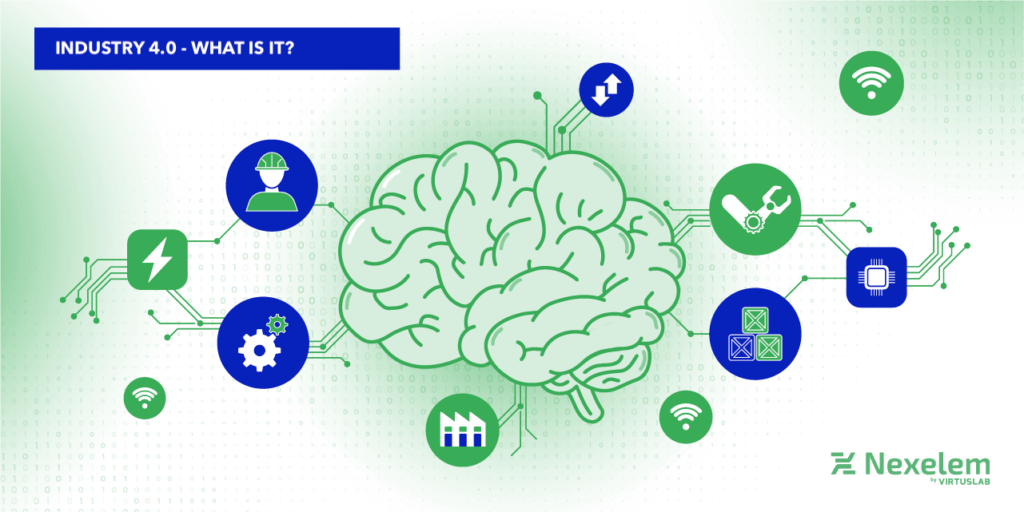
The term Industry 4.0 was first used at the Hannover Messe international trade fair in 2011, when a project developed by the German government was presented. The fourth industrial revolution is the basis for the digital transformation of every company. At its heart are the Industrial Internet of Things (IoT/IIoT) and autonomous systems, which use computer algorithms to monitor and control elements of the physical environment, such as machines, robots or Automated Guided Vehicles (AGV). As a result, every element of the supply chain (production, logistics, warehousing) becomes ‘smart’. It also increases the level of process visibility and control.
The Fourth Industrial Revolution aims to integrate physical and digital assets by harnessing the power of data, analytical tools and mobile technologies in all areas of life. Previous industrial revolutions spanned several generations. Today, wireless connectivity, automation, artificial intelligence, nanotechnology or big data are developing at an unprecedented pace. All this is changing not only the way we live and work, but also the way we relate to each other.
Industry 4.0 is the integration of intelligent machines, systems and the way in which changes are made to production processes. All to achieve better productivity. The impact of the industrial revolution on businesses has been enormous. Not only has the way we work changed, but so has the role of people.
What technologies are driving Industry 4.0?
Industry 4.0 is a revolution in the way products are manufactured, improved and distributed. Companies are integrating enabling technologies such as the Internet of Things, cloud computing, artificial intelligence and machine learning into their production facilities.
Smart factories use advanced software and robotics to make better decisions based on the data collected. Increased automation leads to new levels of efficiency and responsiveness to customers.
The result is higher productivity and better quality. Production errors are also reduced, saving time and money. Importantly, Industry 4.0 technologies can be applied to all types of industrial companies. The most important of these are:
Internet of things
Internet of Things (IoT) – simply put, a system of electronic devices that can automatically communicate and exchange data over a network without human intervention.
IOT is related to IIoT, which stands for Industrial Internet of Things. These are the two main technologies of the digital revolution. The IoT, as a network of connected devices, gives them the ability to communicate with each other and share data with users via the Internet. Everything in a factory can be part of it: machines, electrical substations, buildings, infrastructure.
In fact, the number of connected devices is growing every day. IoT collects data from different sources and then sends the result to a central system via the Internet. This enables managers to make faster and more accurate decisions. It can also predict future outcomes. This technology can be used to automate equipment and some operations. For example, the smart sensors on welding machines can adjust operations to optimise energy consumption, etc., but the simplest example is motion-activated lighting.
Cloud Computing
Cloud computing – is the cornerstone of virtually every Industry 4.0 strategy. To be fully realised, smart manufacturing requires the connectivity and integration of production, supply chain, sales and services.
This is made possible by the cloud, which makes the process of storing and analysing data more efficient and cost-effective. For small and medium-sized manufacturers, the cloud means a real reduction in start-up costs. Cloud computing involves providing computing resources in the form of applications to data centres on demand over the Internet. You pay for what you use. Access to all necessary IT resources is self-service. Cloud applications run on “cloud” computers that are owned and maintained by service providers. Users typically connect to them via a web browser.
AI and Machine Learning
AI and machine learning – Artificial intelligence enables machines to learn from experience, enabling manufacturing companies to make the most of the full volume of information generated on the shop floor, from business units, partners and other external sources.
AI enables the generation of information in terms of visibility, automation and predictability of business processes. One example is in-process failures, which are used to gather information for predictive maintenance based on machine learning algorithms.
This improves business continuity and machine performance. AI is based on the potential of computational units to replicate human learning, first through imitation and then through analysis. In this way, machines can perform tasks that would otherwise be performed by humans. This solution is increasingly used in manufacturing and industry. It is proving its worth in design, improving processes, preventing wear and tear on machinery and optimising energy use. It also plays an important role in quality control.
In a Pandemic survey, 74% of the companies surveyed confirmed that artificial intelligence solutions had proved useful. Investment in digitalisation and artificial intelligence is the current direction for most companies.
Edge processing
Edge processing – the demands of real-time production operations mean that in some cases data needs to be analysed as it is generated, at the edge. This minimises the time between when the data is generated and when a response is required. An example of this would be the detection of a safety-related fault that requires an action to be taken using real-time equipment. In this case, the time it takes to transfer the data to the enterprise cloud and back to production is too long. It also depends on the stability of the network. Edge processing will definitely reduce security risks. The benefit is faster access to insights, faster response times and better use of bandwidth. Data is processed and analysed closer to the point of origin, reducing delivery times.
Cyber Security
Cyber security – the importance of cyber security to manufacturing companies is growing. Operational technology, i.e. the connectivity of equipment in the factory or in the field, enables more efficient production processes. On the other hand, it exposes access points for malware. The digital transformation to Industry 4.0 must be based on cybersecurity. Adequate security measures must be in place for data and cloud services. Stored data must be encrypted and software updated. In the European Union, mandatory certification and accreditation is being introduced to cover IoT devices. Minimum security requirements will be imposed on manufacturers. In this context, risk awareness among company managers and employees is very important. It is not only data loss that is at risk, but also privacy.
Digital Twin
A digital twin is a virtual replica of processes, production lines, factories and supply chains. It is created by capturing data from IoT sensors, PLCs and other internet-connected devices. Digital twins are used by manufacturers to increase productivity. This improves workflows and designs new products. Production process simulation is used to test process changes. It helps develop methods to reduce downtime and increase production capacity. Constant monitoring of the product and its reactions allows continuous improvement and elimination of errors that occur. Optimisation leads to a more perfect product. The digital twin changes the way a company is managed and operates. This brings economic benefits to the business and makes the plant more competitive in the marketplace.
Examples of Industry 4.0 applications
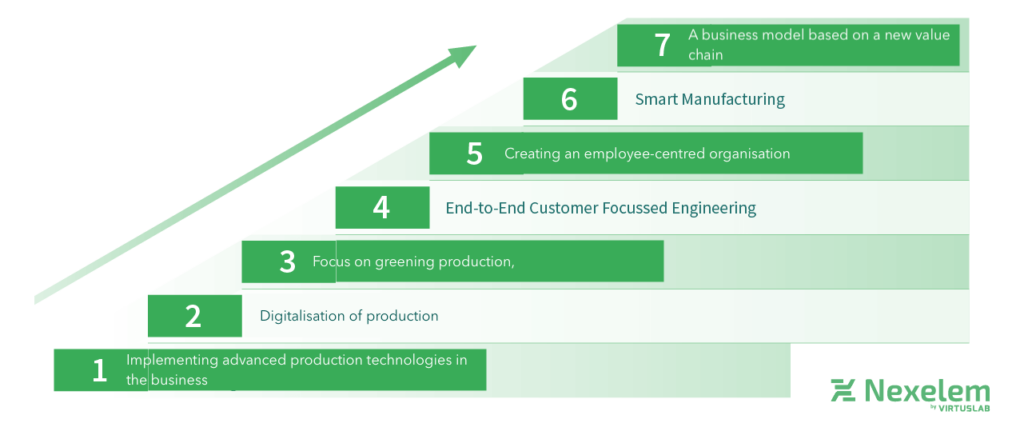
The emergence of digital technologies, together with breakthroughs in materials production and biotechnology, is leading to entirely new ways of producing, communicating, consuming and moving. These changes are fundamental to today’s industries. They affect not only the major market players, but also the entire global economy in terms of local communities and individual identities.
The European Centre for Advanced Manufacturing Assistance (ADMA), set up by the European Commission, is responsible for developing and implementing elements of Industry 4.0. The aim is to facilitate entrepreneurs’ access to technological and organisational expertise. According to ADMA, examples of transformation towards Industry 4.0 include seven stages:
- Implementing advanced production technologies in the business – flexible production systems are expected to facilitate rapid adaptation to changes in the number or category of products.
- Digitalisation of production – people, machines and products need to work together,
- Focus on greening production, e.g. by using renewable energy sources, making full use of raw materials and reducing emissions.
- End-to-End Customer Focused Engineering, i.e. the end-to-end implementation of customer expectations for products.
- Creating an employee-centred organisation – using individual differences to strengthen the organisation and create a friendly working environment.
- Smart Manufacturing – also known as Intelligent Manufacturing, which involves the use of integrated systems that respond quickly to changing conditions.
- A business model based on a new value chain – a factory that is open to understanding the needs of all participants in the process.
What are the benefits of implementing Industry 4.0 in a company?
The Fourth Industrial Revolution requires a new way of looking at the changes taking place, regardless of industry, system or community. A new way of thinking is required to enable companies to achieve the right financial results, taking into account the right place of humans in the world of modern technology.
We already know what Industry 4.0 is, so what are the benefits of implementing it in a company? First and foremost, it makes the company more competitive. Investing in technology and modern solutions significantly improves processes, which brings a new quality of service to customers. It also makes employees more efficient and easier to solve potential problems. Interdepartmental collaboration is strengthened, and the wider use of real-time data helps to make faster and better decisions. Other benefits include
- Increased productivity and automation – Forecasting becomes more accurate, on-time delivery increases, and plans are optimised for profit,
- Greater flexibility in a changing market – advanced planning allows you to digitally transform your supply chain,
- Ability to test new business models – an opportunity to reduce costs and increase efficiency,
- Achieve an environmental goal – allowing you to implement green solutions without sacrificing profits.
The current transformation seems to be one of the most important as it touches every aspect of our lives – work, health and human relationships. Industry 4.0 is based on intelligent, connected technology, both within organisations and in everyday life. Most decisions are shifting to the competence of machines, blurring the line between the biological and the digital. Breakthroughs are also characterised by having a disruptive as well as a creative impact. They offer new opportunities as well as risks. One example is the changes in the labour market that are leading to the disappearance of many traditional jobs.